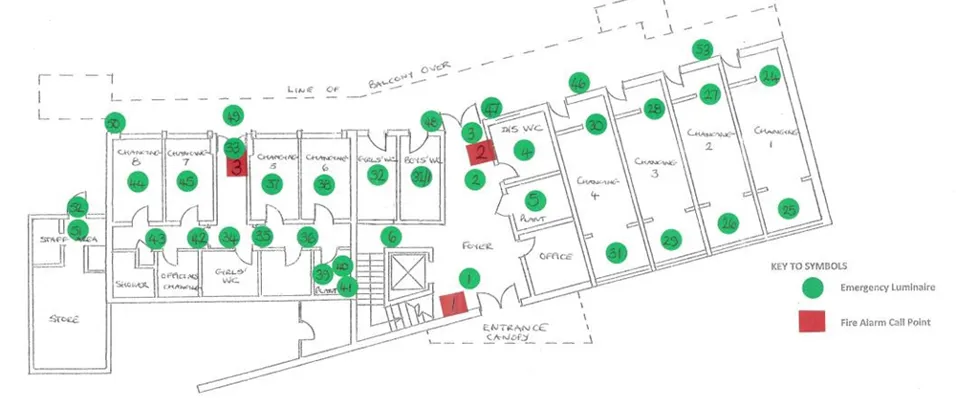
Setting up a basic electrical maintenance regime
To many people, the concept of electrical maintenance conjures up nothing more than failed lamps being replaced. A good maintenance regime however needs to cover so much more.
This article attempts to give an overview of basic electrical maintenance activities, as may befit a typical installation serving a small/medium-sized commercial premises. Activities relating to large scale industrial or specialist installations are beyond its scope, although many of the concepts would apply.
It is important with the imminent re-occupancy of many places of work after lengthy Covid shutdowns that steps be taken to ensure that electrical installations are thoroughly checked and any outstanding maintenance brought up to date. This is a basic safety requirement.
Benefits
Many electrical systems now play a significant role in the decarbonisation and sustainability agenda, but such systems need regular monitoring to ensure they are still performing as intended over their lifecycles and hence providing the energy savings intended.
Effective maintenance can also provide other benefits, some of which are not immediately apparent:
- longevity and improved life cycles of equipment
- reduction in downtime
- end-user confidence
- equipment manufacturers’ warranties being upheld
- fulfilment of legal obligations.
Legal obligations
Legislation is a driver regarding the maintenance of electrical installations and equipment in places of work.
Whilst some may argue that an electrical installation only deteriorates with usage, sometimes the opposite is true – particularly with buildings that may have been out of service for prolonged periods, infrequently occupied or where upkeep may have been neglected.
The Health & Safety at Work Act (1974) places the duty of care on employers, employees and the self-employed to provide for health and safety at work premises. Electrical installations fall under this.
The Electricity at Work Regulations (1989) under its Regulation 4, requires electrical systems to:
- be safe at all times to prevent danger,
- be maintained to prevent danger,
- have work activities relating to them to be carried out in such a manner to prevent danger,
- comprise of equipment which is suitable for its use, be maintained in a condition suitable for that use and be properly used.
Download The Electricity at Work Regulations 1989. Guidance on Regulations [PDF, 336KB]
The Regulatory Reform (Fire Safety) Order 2005 sets requirements for firefighting, fire detection, fire escape and emergency lighting. It requires the ‘responsible person’ for the building to ensure that equipment and facilities associated with these provisions are maintained and kept in a good state of repair.
The Provision and Use of Work Equipment Regulations 1998 (PUWER) requires equipment that is provided for use at work to be suitable for its intended use, safe for use, maintained in a safe condition, inspected regularly and used by persons that have been adequately trained.
The regulations apply to machinery, appliances, apparatus and tools.
Workplace (Health, Safety and Welfare) Regulations 1992 and The Management of Health & Safety at Work Regulations 1999 may also be relevant.
Health and safety regulation... a short guide [PDF, 366KB]
BS 7671:2018+AMD 1:2020 (The IET Wiring Regulations) devotes its Chapter 34 to maintenance. Regulation 341.1 requires the electrical designer where possible to select suitable materials and equipment based on likely maintenance.
Elsewhere, Regulation 301.1 requires suitable equipment appropriate to external influences to be provided.
Continuity of service
A good electrical maintenance regime isn’t just about ticking boxes relating to legislative requirements.
The consequences of an electrical breakdown should play a crucial part in determining the level of maintenance that will be needed. Without a fully functioning electrical installation, commercial or industrial activities can be interrupted. Consequently, it should be the owner of the installation who has to determine suitable risk-mitigating measures.
Developing a strategy
One of the first steps to take will be to consider the pattern of maintenance required. Consequences of failure may set the parameters. Do not forget that as installations change in use or design, then maintenance planning and policies must adapt too. Good maintenance should be driven by a robust maintenance management structure.
The basic criteria are to consider if it will be acceptable to wait and then deal with a failure after it has happened, or if steps need be taken to prevent a failure occurring in the first place.
Life safety systems, such as fire alarms and emergency lighting, are expected to offer a high level of reliability and if failing in an occupied building could lead to far more significant consequences than perhaps failure of general lighting or small power provisions in a seldom-used room.
Applying this concept leads to consideration of the following fundamental categories:
Preventative maintenance
This is maintenance that attempts to prevent a failure occurring in the first place, often referred to as a ‘fix before failure’ regime. This approach would apply to life safety systems, but could equally be applied to other systems, where there may be factors, perhaps operational or commercial which support it.
A good example here would be replacing all the high level lamps in a large hall or public building, where access to the area is not always convenient, as well as the practical issues associated with setting up access equipment. Such an approach can sometimes seemingly fly in the face of sustainability but can offer overall benefits if properly implemented.
Reactive maintenance
Maintenance of this nature is generally waiting for an item or system to fail and then dealing with it individually, in the process ignoring any drop in its performance. Such an approach would be wholly unsuitable with life safety systems or in business-critical areas, but the concept can help win the sustainability argument.
Further considerations in this respect would be shaped by considering the likelihood of several visit per breakdown together with the associated cost. This may not be economically viable in some instances, although the benefits of keeping selected spares on site may assist.
Predictive maintenance
This approach monitors a system, accepts some individual failures which are tolerable, but then at a given point, deals with issues before complete failure. An example here would be to wait for a certain percentage of lamps to fail and then renew lamps to all luminaires. Such an approach could help balance sustainability weighed up against practicalities and cost.
Careful monitoring is a key factor in this method – which may need to feature regular inspections or perhaps hours-run data being collated. More complex systems could monitor via automated systems.
Documentation & record keeping
Before commencing any maintenance regime, detailed information and records need to be pulled together.
Broadly speaking, such information can be split into three categories:
Information regarding the buildings and the site
This should include layout plans for the premises where the maintenance will be required and may need to be of sufficient size and scale to detail the equipment being maintained.
Such plans could already be in existence, perhaps as having been produced in the past as part of 'Operating and Maintenance' (O&M) manuals, or from previous maintenance activities.
Very often, no information is available – in which case it should to be produced. This may be either from scratch via site survey or based on information that could be available elsewhere, such as legacy drawings that have been produced for other purposes.
In all cases, information needs to clearly show what requires maintenance – especially critical items like fire alarm or emergency lighting equipment – and where it is located. Such equipment, or ‘assets’ depending on the complexity of the installation, may benefit from unique referencing or tagging. This aids traceability – especially if multiple operatives carry out the maintenance work, but also for overall management of the regime - and of course auditing!
Figure 1: Simple layout drawing showing uniquely referenced emergency lighting and fire alarm call points
Information relating to equipment on the site
An asset list detailing equipment on site should then be drawn up. The complexity of the installation will dictate how detailed it needs to be. Again, this may be available in the form of existing O&M information languishing somewhere on site. Enquiries may prove fruitful and save much work.
Good O&M literature should ideally contain sufficient information detailing maintenance requirements and operating information, but this is not always the case. Additionally, lists of spares, etc. – as well as the manufacturer’s contact details may be included. Such information may be hopelessly out of date. In this case manufacturer’s archives could be sourced, or, if nothing else, generic information be gathered.
It may even be that asset details are held elsewhere in a company – for perhaps financial or tax planning reasons. Again – keep asking questions!
Record logs of maintenance activities undertaken
Once a new maintenance regime has commenced, information is needed that accurately records the activities actually carried out.
As a minimum:
- the individual services being maintained, including details of when a task is due and what it entails
- records of site visits – showing date, tasks completed, operative responsible and any follow up works needed
- meter readings to monitor energy consumption. (Note -Fitment of additional meters may assist with this).
Such information is the key to:
- be able to monitor and control any maintenance contract in place
- enable effective maintenance to take effect, especially relevant where multiple operatives are involved
- to assist in future maintenance planning
- to monitor energy consumption and assess plant condition
- to be able to prove that legal obligations have been met.
An additional and often overlooked benefit here is that BS 7671:2018+AMD 1:2020, under its regulation 652.2, allows effectively managed preventative maintenance to negate the need for separate BS 7671 periodic inspections.
In-house or outsourced?
Once it has been decided that maintenance will be needed, in what form that maintenance will take and the documentation gathered, the next decision to make will be whether the work is to be carried out by in-house staff (either already employed or newly acquired), outsourced to specialist providers or use a mix of both.
This decision-making process would be driven by:
- the scale and complexity of the systems needing maintenance
- consequences of failure
- overall commercial viability.
Further factors that may steer any decisions may be:
- skill set and competency of any existing staff already on site
- whether in-house staff (either existing or newly employed) could be utilized in other parts of the business and/or trained accordingly
- procedures/policies or other contracts in place, perhaps in other parts of the business.
Life safety systems such as fire alarms, or any system of a more complex nature, will likely have very specific maintenance needs, often defined in continually-evolving industry standards and codes of practice. Specialist testing and inspection equipment and techniques are often also needed. Modern systems may also incorporate access codes and software functionality as well as having warranty stipulations. Such factors are important to address when considering who is to undertake routine service and maintenance.
Regardless of how the maintenance is resourced, remember that Regulation 16 of the Electricity at Work Regulations (1989), requires persons to be competent to prevent danger and injury.
The remainder of this article is intended to act as an aide-mémoire, covering the type of electrical systems that often require maintenance and considerations to make.
Electrical systems requiring maintenance
Fire alarms
Fire alarm systems, as one of the principal life safety systems in a building, have very specific defined maintenance needs.
Apart from on very basic manual systems, any party contemplating such work, would need a detailed knowledge of BS 5939-1:2017 ‘Fire detection and fire alarm systems for buildings’. Section 6 of this standard defines maintenance, recognizing that it will cover aspects ranging from daily user checks through to very specific tasks at stipulated intervals.
At the outset of a new fire alarm maintenance regime, a detailed inspection of the premises should be made, as well as its fire risk assessment document, to assess:
- any specific system needs, matched to building layout, usage and escape routes
- existing fire alarm system, previous records or logs and any evidence of departures from BS 5839-1:2017.
Once this has been undertaken, where required:
- provide a site log book if not in place
- carry out repair of any existing faults or damage
- make arrangements for responding to emergencies, agreeing required response times.
At this point, the ongoing regime can be formulated, to include:
- weekly manual call point (and if applicable, voice alarm) tests
- monthly tests and checks on power supplies and review of log book entries
- quarterly detailed checks of certain battery systems
- six-monthly checks/tests – of logbooks, building usage, call points, automatic detectors, false alarm records, battery condition, correct operation of control and signaling equipment
- annual checks to at least cover radio signalling, cause and effect operations and accuracy of zone charts and unique identification of all devices.
Further information can be found in the new forthcoming 3rd Edition of the IET’s Electrician’s Guide to Fire Detection and Fire Alarm Systems.
Emergency lighting
Emergency lighting, also a life safety service, has essential defined maintenance needs. As with fire alarms, firstly, the premises’ Fire Risk Assessment document should be studied.
The following two standards apply:
BS 5266-1: 2016 ‘Emergency lighting. Part 1 Code of practice for emergency lighting of premises’
BSEN 50172: 2004 (BS 5266-8:2004) ‘Emergency escape lighting systems’
Sections 12 and Section 7 of these respective standards require:
- daily checks of charge indicator lights where applicable
- monthly short duration tests of lighting on a simulated supply failure
- annual tests of all lights, for their full rated duration, as well as detailed visual examination.
Maintenance should include logging of all results, follow up repairs, as well as works that may apply to central battery systems or other standby supplies such as generators. Unique identification of all equipment is necessary.
Consideration should be given when undertaking full duration tests, of the need for battery-driven systems to recharge, before such lighting can again become fully effective. Such tests should therefore consider building occupancy immediately following the test.
Where self-testing or so-called ‘intelligent’ systems are encountered, it will be essential for the maintainer to be fully aware of exactly how the system operates, and especially what respective indicators mean as these may differ depending on the manufacturer.
Non-internally illuminated escape signage should be checked for adequate illumination and cleaned where necessary.
Detailed record keeping will reinforce the evidence that tasks have completed as well assisting long term with any predictive maintenance work, such as planned battery or lamp replacements.
Further information can be found in the IET’s Electrician’s Guide to Emergency Lighting.
Other alarm, signalling systems or monitoring systems
Other alarm or monitoring systems - sometimes life safety-related - are often encountered. These should be maintained to ensure continued reliable operation.
Examples may include:
- gas or carbon monoxide detection systems
- security and intruder systems
- CCTV systems
- lift alarm systems
- disabled toilet alarms
- personnel alarms
- access control systems
- class change systems
- building services control systems & building management systems.
Routine maintenance should follow the manufacturers’ requirements.
Lightning protection
These systems will require specialist knowledge, access, and test equipment to maintain. Consequently, these activities are best entrusted to specialist providers.
BS EN 62305-3: 2011 ‘Protection against lightning Part 3 - Physical damage to structures & life hazard’ - Section 7 and Annex E7 defines maintenance and inspection requirements.
Typically this would include checks for:
- system components in good order, (not corroded, damaged, or subject to theft)
- system compliance with the relevant design standard
- earthing continuity.
Although such an inspection is often undertaken annually by default, best practice is to arrange for visits at differing intervals, which enables the system to be evaluated at varying times of year, where ground and climatic conditions may have a bearing on system performance. Surge protection devices (SPDs) must not be overlooked. These are designed to protect electronic equipment of the building’s electrical installation and should also form part of this regular maintenance regime. If no lightning protection is provided SPDs should be checked with the fixed wiring installation. All SPDs should be checked against their specific manufacturers’ instructions – especially regarding indicator status and fuse protection.
Fixed wiring installation
Electrical installations deteriorate with time and usage. The concept of periodically inspecting and testing a fixed wiring installation should feature strongly in any maintenance regime - either as part of defined preventative maintenance tasks or as a stand-alone activity. BS 7671:2018+AMD 1:2020 covers this in its regulations 135.1 and 652.2 as well as guidance in its Part 6 and Appendices.
Such an inspection by a competent person will include visual checks and detailed electrical tests and measurements. The outcome, especially if a stand-alone exercise, will usually be recorded on an Electrical Installation Condition Report (EICR).
Guidance on this topic can be found via the following PDF:
Figure 2: Visual checks of circuit details before electrical testing
The IET’s BS 7671 Guidance Note 3 gives more information on undertaking the actual tests as well as suggested initial frequencies. The person undertaking the inspection should determine subsequent testing frequencies, based on the condition and use of the installation.
Where larger switchboards or control panels are encountered, BS 6423: 2014 ‘Code of practice for maintenance of low-voltage switchgear and controlgear’ should be referenced.
Due to the need to isolate supplies to complete tests, careful planning will be necessary, which may involve the input of many parties and end users. The concepts of splitting the inspections over time may help, particularly on larger sites. When adopting this approach careful planning will be needed to ensure no area is subjected to excessive timescale between inspections.
Sampling is another concept but can be open to errors and abuse and as such is not considered best practice. If a sampling approach has to be used, it will be essential to involve all stakeholders at the outset, and clearly detail what is included and excluded, being mindful of long term risks and liabilities.
Thermal imaging checks, subject to safe methods of working can also feature in an inspection regime – but only where the equipment to be checked is suitable.
Lighting installations
Despite the widespread shift to LED-based lighting solutions which claim longer life and elimination of traditional lamp changing, lighting maintenance cannot be disregarded.
Equally, maintenance-hungry non-LED luminaires are likely to be encountered for many years to come.
Lighting will vary considerably depending on application, and contribute a life safety role with certain critical tasks, as well as general personnel security and safety.
Regardless of the technology used, the performance of all lighting will deteriorate over time, this process usually going unnoticed until complete failure. Lighting designers refer to this concept as ‘maintenance factor’ and when designing take into account issues such as lamp technology, environment in which the lighting is provided as well as intervals between cleaning. Maintenance should acknowledge this, but often doesn’t!
All these aspects will feature strongly when setting up a proposed regime, balancing maintaining lighting efficacy against the practicality of accessing the luminaires in question.
Figure 3: High-level lights – needing specialist access equipment and the area vacated
Practicalities include:
- safe working practices – especially when working at height; fittings may have large physical dimensions or weight, and/or may be situated in areas with either pedestrian or vehicular traffic adjacent
- access to a given area, with sufficient time to safely erect scaffolds, access platforms etc
- electrical isolation and lock-off – particular where supply is remote
- fire integrity – especially relevant with recessed luminaires in certain ceilings
- lamp disposal – glass breakage risks as well as disposal aspects under WEEE legislation.
It is for these reasons that a ‘preventative’ rather than ‘reactive’ maintenance regime can sometimes prove beneficial.
Appliances
Electrical appliances provided in a place of work will require inspection, testing and sometimes maintenance. Where applicable PUWER regulations will apply.
Although colloquially referred to as ‘PAT testing’ and very often assumed to be an annual task, there have been recent changes to guidance and requirements.
The latest version of the IET’s Code of Practice details further.
Remember that with built-in or permanently connected equipment or appliances, for example, water heaters, cookers, air conditioning, fans, refrigeration, etc. it will be essential to ensure that these items do get checked!
Solar photovoltaic (PV) power supply systems
These systems are seldom maintenance free and should be regularly inspected and maintained by a specialist provider.
Inspections would normally check for equipment damage, fixings, cleaning and system performance monitoring.
Electrical testing should also be undertaken to ensure continued safety.
Further guidance can be found in the IET Code of Practice for Grid-connected Solar Photovoltaic Systems
Lifts
Maintenance of lifts is a requirement under Regulations 5 and 10 of the PUWER regulations. The extent of the maintenance will depend on the lift type, its age and condition. Invariably this work should be entrusted to a specialist lift maintainer, often included as part of an all-embracing servicing, maintenance, and call-out contract.
In addition, regulation 9 of the Lifting Operations and Lifting Equipment Regulations 1998 (LOLER) requires a ‘thorough examination and inspection’. For passenger carrying lifts this is at least every 6 months, and for other lift types it is at least every 12 months.
Further guidance can be found in the PDF below:
Waste Electrical and Electronic Equipment (WEEE) Regulations 2013
Maintenance of electrical installations invariable involves the removal and safe disposal of spent or failed equipment, especially lamps. Most supply-chain providers offer facilities for dealing with such waste products. Alternatively, most local councils can be approached.
More details can be found on the Electrical Safety First website.
Summary
This article has shown that there is so much more to electrical maintenance than just replacing lamps!
As well as a myriad of legislative requirements needing to be met, robust electrical maintenance ultimately leads to increased levels of electrical safety and efficiency.
With many buildings now seeing increasing occupancy and use once again, now is definitely the time to put such work on the agenda, and for those who can provide such services, there will be increasing business opportunities.
Further reading on this wide-ranging subject can be found in:
- BS 8210:2020 Facilities maintenance management. Code of Practice
- BSRIA BG53 Business-focused maintenance
- The IET’s Guide to Electrical Maintenance