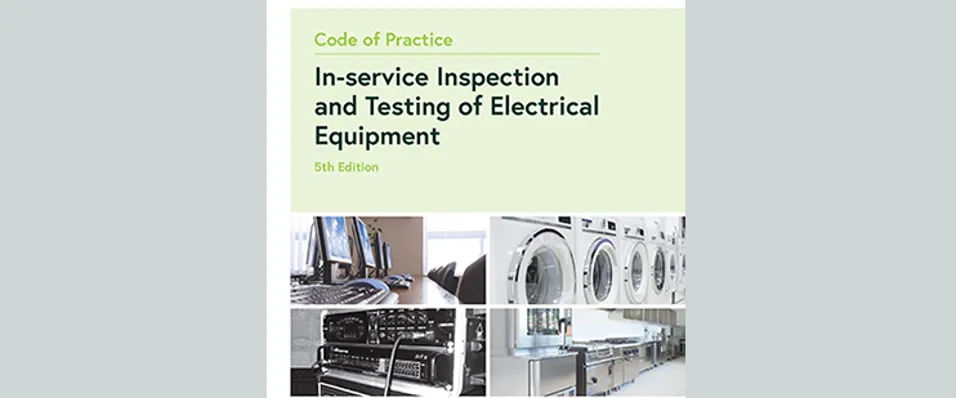
The all-new 5th Edition of the IET Code of Practice for In-Service Inspection and Testing of Electrical Equipment
Readers will undoubtedly be familiar with ‘PAT testing’ as a concept – if not in practice, then certainly as an observer of electrical equipment in the workplace sporting the ubiquitous green ‘pass’ label or similar. The origins of this process can be traced back to the 1st Edition of the IET Code of Practice for In-Service Inspection and Testing of Electrical Equipment (commonly referred to by many by the easier-to-pronounce acronym ‘COPISITEE’), which this year sees quite a significant revision.
History of the Code
Before giving an insight into the proposed changes contained within this latest revision, it is interesting to reflect on the origins of the Code, first published in 1994. When the Electricity at Work Regulations (EWR) came into force in 1989, the subject of electrical safety management was debated and in particular, how businesses could comply with the requirements of the Regulations in the workplace. It was acknowledged that the design, construction and maintenance of most electrical installations were adequately catered for in the (then) IEE Wiring Regulations, but this left the question of how to manage all the equipment connected to the installation itself.
The IEE formed a working group to look at the issue, comprising many representatives from industry, including appliance manufacturers and trade associations. As a starting point of reference, manufacturing representatives detailed the electrical safety tests that are conducted on appliances at the time of manufacture, as required in product safety standards. These were subsequently used as a basis for the 1st Edition of COPISITEE, as a means of verifying the ongoing electrical safety of appliances. Thus, ‘portable appliance testing’ (PAT) was born….
Those familiar with previous editions of the Code will have seen that these origins are fairly prevalent throughout, with, for example, appendices detailing the requirements of appropriate product standards. Over time, as data about the effectiveness of appliance testing became available, it was accepted that not all the tests were really suited to routine maintenance; older readers might remember the ‘hi-pot’ or flash test and microwave leakage tests, for instance.
In successive editions, changes aimed at moving towards the original intent of verifying the safety of electrical equipment for continued use were made. A clue to the change of focus in the forthcoming edition can be found in the title of the COPISITEE itself, which is often overlooked: ‘In-Service Inspection and Testing of Electrical Equipment’.
Appliance or equipment?
While the industry is familiar with portable appliance testing, generally the approach in most workplaces is simply to check those things fitted with a plug that are – to varying degrees – ‘portable’. An appliance, however, is actually defined in standards as “apparatus intended for household or similar use”, which of course excludes many types of electrical equipment found in the workplace. It’s also noteworthy that generally, the EWR does not apply at home in a domestic setting, with a few limited exceptions. It can be seen that use of the word ‘appliance’ is not representative of what the COPISITEE seeks to embrace, namely ‘electrical equipment’ that is ‘in-service’, i.e. used at work.
Looking at ‘electrical equipment’, this is actually defined in the Code as an “Any item for such purposes as generation, conversion, transmission, distribution or utilization of electrical energy, such as machines, transformers, equipment, measuring instruments, protective devices, wiring systems, accessories, appliances and luminaires.”. Electrical equipment, therefore, includes appliances such as washing machines and vacuums.
This is a definition that is fairly all-encompassing, including within it most (if not all) of the items of electrical equipment to be found in a workplace. For this reason, the forthcoming 5th Edition of the Code places a much greater emphasis on the original intent of managing electrical equipment in the workplace that is not covered under other maintenance regimes, such as the electrical installation itself. The equipment may not be fitted with a flex and plug and could be wired into the installation, such as an air-conditioning unit or a security access control system. These types of equipment often fall through the gap of in-service inspection and testing, with the person conducting the Electrical Installation Condition Report (EICR) stopping at the fused connection unit or isolator supplying the equipment, and the ‘PAT’ tester seeing it as part of the installation itself, and not a portable appliance.
The 5th Edition of the COPISITEE, therefore, makes no mention of the words ‘portable’ and ‘appliance’, other than in the explanatory notes in the preface. In fact, another allied change is the removal of the terms ‘stationary’, ‘portable’, ‘fixed’ and ‘moveable’, as the key focus is on the verification of equipment for safety in continued use. The equipment’s ability to move or be relocated (or not, as the case may be) doesn’t affect the nature of the testing and inspection required, although it might have a bearing on the frequency of the maintenance activity.
The changes in brief
The 5th Edition is a significant departure in respect of layout too. Previous editions were broadly split into two sections: the first concerning the management of electrical safety and the legal requirements, and the second aimed at the person conducting the inspection and testing, comprising the test requirements, visual inspection checks and more.
Approximately 26 years on from the 1st Edition of the COPISITEE, the need for management of electrical safety in the workplace is better understood and the structure of the Code has thus been revised into a series of sections, taking the reader through the need for electrical maintenance, the legal requirements, the competencies of those conducting the work, types of equipment and tests, as well as a section on the frequency of inspection and testing. New appendices include guidance on low-risk equipment and environments such as IT server racks; a basic electrical theory primer; a workplace poster for user-checks and example risk assessments for ascertaining the frequency of testing.
The revision also reflects modern equipment and practices, with commentary on second-hand and hired equipment, as well as on the perennial issue of equipment that may be fake or sourced from suppliers where its provenance may be in doubt.
In recent years, there have been changes to product manufacturing standards, in which the methods of providing protection from electric shock have been reclassified and changed. Readers may be familiar with separated extra-low voltage (SELV), for example, where protection against electric shock is provided by electrical separation from earth and other circuits, coupled with extra-low voltage. This has been widely used in Class III equipment but is no longer a method of protection prescribed in BS EN 62368 Audio/video, information and communication technology equipment, which has combined and replaced other common product safety standards.
The classifications for safety are now described as ‘energy source classes’, which is subtly different to the previous methods of description. While to the end-user the changes may be of little consequence in practice, it is important that those performing the inspection and testing of electrical equipment understand the new classifications. Confusingly, SELV is still a valid method of protection for electric shock when used in an electrical installation (i.e. one complying with BS 7671 Requirements for Electrical Installations), but it is no longer a valid method for an item of equipment. The distinction is important to understand, especially when selecting products that may be used in an installation requiring SELV as a protective measure. The 5th Edition of the COPISITEE has been updated to reflect these new classifications.
The conducted tests are another area of change, with the inclusion of a flowchart to aid those performing the inspection and testing to select appropriate tests according to the equipment. Again, the focus has been on the verification of equipment for electrical safety for continued use, and this has led to the list of required tests being revised. For example, some items of Class II equipment may no longer require testing, with a visual inspection being satisfactory on its own. The high-current earth bond test has given way to a preference for a lower-current one, because empirical evidence suggests that the higher current does not stress the connections as much as first thought, given the duration of the test. The insulation testing voltage has also been revised, taking into account the design of modern electrical and electronic equipment.
A significant change (perhaps the most significant, depending on your view!) is a complete review of the frequency of testing, currently exampled in Table 7.1 of the 4th Edition. This table disappears in the 5th Edition, although if you want to know what it has been replaced by, you’ll have to wait for the next instalment of this article, due in the September issue of Wiring Matters (issue 82).
The 5th Edition of the IET Code of Practice for In-Service Inspection and Testing of Electrical Equipment is currently due for publication in September 2020, although given the ongoing Covid-19 situation, the date may shift somewhat. It is possible to pre-order a copy via our online shop.