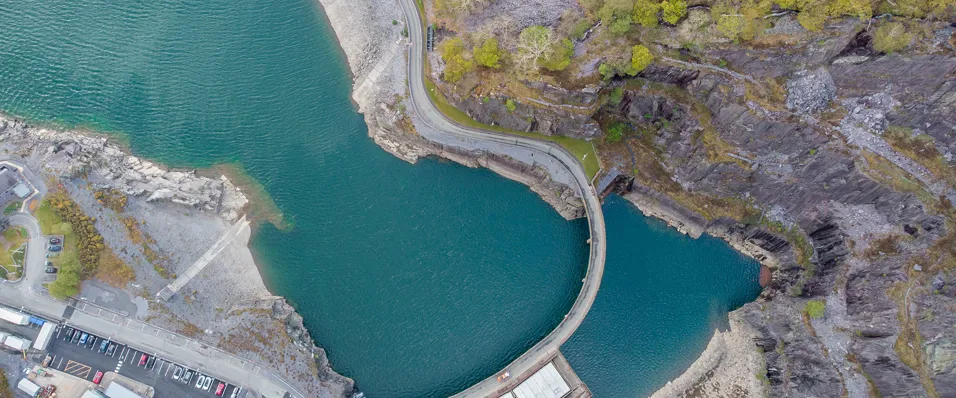
DC Realisation in the 21st Century
The first article in this series outlined the history of electricity distribution and the losses entailed with distribution via the AC grid equipment we have in service now.
Introduction
This article will outline some ways DC fixed wire installations have been implemented in buildings and some considerations for electrical designers wishing to implement, or just be future-ready for, similar arrangements.
Readers should note that this article considers consumer-side final circuits (and some appliances) to be part of ‘the grid’, as opposed to it being the destination of the grid. This blurring of the boundary is the first thing that needs to be looked at if we are to understand the DC opportunity.
For decades, electrical distribution has looked as it is depicted in Figure 1.
Figure 1
In reality, this arrangement would be more like a web with interconnected generators and cables serving all end-use points. However, the arrows shown pointing left to right here would have been accurate in relation to ~99% of the national grid until relatively recently. One notable exception was Dinorwig power station commissioned in 1984 which could use electricity at off-peak times to pump water against gravity to be released again to generate at peak times. Dinorwig’s peak output was 1728 MW, which represents about 6% of our average demand in the UK today. Its contribution can be represented as shown in Figure 2.
Figure 2
Dinorwig arguably represents the earliest iteration of the ‘smart grid’ concept which is revolutionising the energy industry today.
Why DC Now
The argument, and strategy, for morphing the grid to accommodate DC relies on a number of changes since Dinorwig was commissioned including:
1. The exponential increase of places like Dinorwig where significant energy flow can be bi-directional. Much of this is battery energy storage which means it is DC. In February 2021 there was more than 1 GW of operational battery storage capacity in the UK, with a huge increase projected as shown in Figure 3 by REGEN SW.
Figure 3
2. A massive increase in DC assets embedded at the local/micro level in the form of microgeneration (mainly PV) and battery energy storage.
3. On the subject of Battery Energy Storage we cannot ignore EVs. International standards are being developed to encourage their use, IEC 60364-8-82, and in particular clause 8.5 “electric vehicles” is intended to give guidance for prosumers’ electrical installations. There are an estimated 370,000 Battery Electrical Vehicles on the road in the UK today. If we ballpark their individual capacity at 10 KWh that gives us 3.7 GWh of storage. If all were to be connected at one time, 370 MW of instantaneous power could be harvested if we took 1KW from each EV. Vehicle to Grid (V2G) technology is in its infancy but we can’t dismiss its potential while considering the architecture of a sustainable grid. That would be equivalent to two Dinorwigs - and electrical batteries can get up to speed a lot faster than Dinorwig’s 16 seconds!
The three points above inform this high-level view of where DC can be found:
Figure 4
Note: Large Wind Turbines typically output AC, they are included in this diagram to reflect their potential to contribute to a stored energy grid.
The diagram shows that we have DC generation and storage on both sides of the Macro Grid. This article focuses on strategies for enabling the uptake of DC on the right-hand side of the macro grid; Utilising DC micro-generation + DC micro storage to create more energy-efficient DC opportunities in the built environment.
This is not to say that the Macro Grid cannot ever transmit DC, it could and in some instances already does, but this article is for a readership that typically is more involved on the ‘micro’ side.
Fixed wire DC installations in the built environment
The previous article in this series explained the status quo. We have a large amount of infrastructure to turn AC into DC and back again over and over but it produces huge amounts of unwanted heat (I2R losses) and energy embodied in billions of manufactured conversion devices. So how can electrical designers help with this clearly undesirable situation?
In 2022 they can create an infrastructure that is AC/DC agnostic. It should be said however that delivering a fully DC domestic or commercial environment is, in 2022, still a very challenging endeavour! Global manufacturing is still set up for AC, not DC, so designing out AC completely is not currently a realistic aim for any but a few specialised pioneers whose work we will come to later in this article.
So the conversation here is about how we can ‘future-ready’
Future-ready factor 1 – Create space for adjustments and later additions, particularly at the origin
If we accept that a transition to DC from AC will not be instantaneous or complete then we are faced with a reality where AC and DC circuits must exist in proximity to one another at least for a time. This situation has existed with respect to band 2 (Low Voltage) and band 1 (Extra Low Voltage, typically telecommunications cables) circuits for decades. The issue of segregation becomes more challenging where we are looking to deliver power to all appliances – not just telecommunications to electronic devices.
Figure 5, taken from the Guide to Smart Homes for Electrical Installers, encapsulates the method that smart home installers already employ to give themselves wiggle-room.
Figure 5
Smart homes typically use 24 VDC for lighting and sensors alongside 230 V AC. Enclosures for this purpose as shown above tend to be much larger e.g 90x80 cm and even with this room to play with option C above will probably get you in a lot of difficulty with segregation.
In many cases a multiple-enclosure approach is taken:
Figure 6
The arrangement above affords extra latitude for segregation and later addition of equipment and cables.
Big plant rooms – in the right place
Having a fabulous cluster of enclosures, what smart home designers call a ‘head end’ at the origin isn’t necessarily going to be enough though. Forward planning is needed to allow for the integration of other related plant which can be harmonised with DC, the possibilities are endless, some of which are shown in Figure 7.
Figure 7
If we consider the scenario in the diagram above with 6 elements in addition to the final circuits for domestic, and seven for commercial – clearly the hallway or under the stairs is not a future-ready location for the distribution board of the future.
Commercial and industrial electrical designers will not need to be told they need to factor in a Plant Room. But do they need to revisit the criteria for sizing, location, and connectivity?
Maybe architects need to be in on this discussion? Consider that a roof without PV is a missed opportunity, but also consider that EVs are coming and that they will function as a load and a supply. The plant room for our DC future needs therefore to be somewhere between the PV and the parking. It also needs some space for some pretty big boxes (which have not been designed yet) and ducting for cables that can manage EV level DC energy.
Future-ready factor 2: what equipment?
Exactly – no one knows for sure.
Two assumptions I will bet on:
- The modern premises already has >90% of the appliances it’s ever going to have and >90% of those are already more or less where they are going to stay within those premises.
- Those appliances that can, will drift over to a form where they can be fed DC direct within the next 20 years. The exception being big thermal appliances e.g., space and water heaters.
So, the prize goes to the designer who can design final circuits for now which can transition from AC to DC when required.
Future-ready factor 3: Which voltage?
A good question with many answers, all with qualifying factors which in turn have their own qualifying factors . . .
Some flags in the ground for now:
- 5 V USB DC is going to be around for a while yet. It is very safe and ubiquitous. It is limited in the power it can deliver and is subject to high transmission losses.
- 700 VDC is the highest DC voltage I have seen proposed for a building designated for habitation. It’s good for cutting transmission losses over distance and therefore better for higher power applications. It is more challenging to make safe for human proximity
- 350 VDC is beginning to resolve as a good level to transmit electricity over longer distances (>10 m) through premises. It would usually be found out of touch range and be galvanically isolated from touchable appliances.
- 48 VDC is beginning to resolve as a good level to step down to from 350 VDC locally to end-user appliances. It’s a happy medium for reasons including:
- Transmission losses (voltage drop) are low enough to make powering appliances like refrigeration viable with standard cable sizes over reasonable distances.
- The voltage level being this low ameliorates some issues that DC can create e.g., the challenge of extinguishing DC arcs when breaking circuits.
- Electronics such as those found in the sensors and processors that smart sustainable buildings need can be adapted to work with 48 VDC. This allows us to have one cable that can serve for power, lights, telecommunications and smart-building gadgets. That’s going to mean less cables and more possibilities – what’s not to like about that!
N.B. While we can say that where all other factors are equal, electrical hazard increases as voltage increases, it is also the case that any voltage can kill given the ‘right’ circumstances. DC installations require specialist earthing arrangements which are not dealt with in this article.
The snake in the woodpile – voltage and the final metre
I have been involved in the delivery of the DC demonstration area within the IET’s refurbishment of its head office at Michael Faraday House. It would be fair to say that the most complicated aspect of this project has been resolving the real-world issues around providing the various pre-specified IT products with the energy they require. In short, the biggest battle has been fought in the final metre between the wall plate and the devices themselves.
We had the benefit of a team of top-flight electronic engineers and it was still a challenge. The issues are too many to list here but will be addressed later in this series. The advice for now is to obtain the full suite of IT equipment intended for DC-direct connection and bench test it before specifying infrastructure to serve it. In time the world’s electronics manufacturers will catch up. But until then, if contracted to handover a working DC environment play safe and bench test before making promises.
Future-ready factor 4: Which cable?
Proprietary DC cables are still niche and so more expensive than standard cables. We do not yet have set Codes of Practice for DC installations. Therefore, it seems reasonable to go on using standard cables for a time.
Bear in mind though that a 500 W appliance running at 230 V will draw 2.2 amps, while a 500 W appliance running at 48 V will draw 10.4 amps.
Increasing all cables current carrying capacity by a factor of 4 will not make for a cost-effective or sustainable installation.
Therefore, either use ample ducting for all runs or give careful consideration to the following…
Future-ready factor 5: Which topography?
Basically, the Ring Circuit is dead. It was fun and easy to live with but we have to leave it behind now. Large oversized circuits to serve general zones should be phased out. Radial circuits targeting specific loads to clusters should be phased in
You must identify where significant loads or load clusters are likely to be and direct appropriate size cables accordingly. Kitchens with kettles and hobs are likely to stay predominantly AC for years to come but bedrooms could be flippable sooner, if not now.
Similarly, try to identify zones that will have just IT or AV equipment and let them have a dedicated cable that can be swapped over to DC later.
Running all final circuits back to a single point will make metering of energy use easier. It will also be a big enabler in terms of functionality, allowing for circuits to be grouped/‘meshed’ to allow efficiency measures like separate circuits for lighting in areas which do not have natural light or having one big efficient central power supply as opposed to multiple less efficient power supplies.
This leads us to our next point…
Future-ready factor 6: Which converter?
Let’s start by making the distinction between an inverter and a converter.
An inverter changes DC current to AC current, a transformer-rectifier does AC to DC and a few devices combine both functions.
A converter adjusts the voltage of DC from one level to another but keeps it as DC.
What we have on premises at the moment is lots and lots of power supplies which are often called transformers or ‘dongles’ which are often integrated into particular appliances e.g. a 5 V USB module within a socket plate or a lump in the line of a laptop supply. These serve to transform 230 VAC into DC at whatever voltage is required by the device. This situation wastes energy as discussed earlier.
In a perfect world with friendly physics, we would have one source or converter supplying all of the DC devices with one DC voltage and they would all be happy - in practice this is challenging to achieve.
Take laptops as an example of the challenge. There is very little variation in the power requirements of laptops and yet we still have a multitude of voltages and connectors for laptops. The same is true of equally ubiquitous monitors and displays. A standard DC voltage for electronic equipment, which by definition needs DC, is still a way off.
The market and manufacturing base for DC appliances like refrigerators is as yet tiny compared to laptops and monitors so the situation is even more problematic for other ‘white goods’ at the moment. Also, the jury is still out on whether 48V DC will emerge as the victor for the wider gamut of DC appliances and devices.
So the advice for the aspiring DC designer for the moment is to claim the space for the bigger distribution board and plant room as described earlier. Ensure enough space to safely patch final circuits through to the converter/voltage they need, when they need it. At the time of writing, the wise designer makes space for multiple voltages.
An alternative approach for larger buildings is to have a DC power BUS at a high voltage and use DC-DC converters to ‘step down’ local to equipment clusters, this approach is explored in the next case study.
Case study 1 – large commercial
Figure 8
The Michael Faraday House DC project has benefited from guidance and equipment from DC Systems based in the Netherlands. Being the leader in innovations for DC applications, they joined forces with the global energy management experts, Schneider Electric. Together, both companies reinforce their expertise in developing safe, resilient microgrid applications
The illustration in Figure 8 shows how the voltage levels described above might be deployed in practice in large commercial premises in which DC Systems specialise in.
Note that the 700 VDC line shown at the top could be run at 350 VDC if distances and voltage drop allowed.
There is a similar line at the bottom. Either would probably be a busbar in practice. Tap offs with converters are used to step down to 48 VDC to serve equipment clusters which here consist of lighting in the ceiling and IT equipment on the floor. It would be possible to supply a host of other sensors and actuators from these converters.
An installation on this scale with this infrastructure would probably incorporate on-site PV and battery energy storage and be capable of providing power for instantaneous hot water taps.
At this scale, trading energy back to a smart grid becomes potentially very attractive.
The plant room for an installation like this could have the capacity for fuel cells and hydrogen storage, and also have some extra space for something that no one has thought of yet.
Using a higher voltage bus and step down architecture requires robust health and safety strategies. This diagram indicates how DC Systems might zone their commercial installations. DC Zone 0 is for qualified technicians only, DC zone 4A is open to all. The zones in between would need to be carefully assessed on a case by case basis.
Figure 9
Case study 2 – domestic expert enthusiast
Figure 10
The illustration above is a grab and simplification of a diagram of a working installation designed and installed by a member of the 48 VDC realisation forum.
The PV panels shown on the right operate at 48 VDC.
The BYD battery at lower right is also 48 VDC
Together they constitute a stable supply to a 48 VDC busbar.
In this arrangement, they feed the property via an inverter charger which ensures the 48 VDC battery remains charged and converts 48 VDC to 230 VAC when required by the house.
This arrangement effectively bridges the current lack of affordable 48 VDC appliances.
When they become available, the wiring could be adjusted to supply 48 VDC direct without conversion losses.
There is no need for a 350 or 700 VDC busbar in this instance because the reduced distances do not present severe voltage drop problems. Higher current loads should be designed as close to the origin as possible and specified with larger cables.
This kind of adaptability relies on a well thought out and provisioned distribution centre and overall installation.
Case study 3 – the Open DC Grid
Figure 11
Not a case study in the same sense as 1 or 2 but illustrative as an example of how one faction visualises a DC energy world. In this scenario 48 V DC is the maximum and everything has to live under that ceiling. This fits well with case study 2 but case study 1 becomes a high voltage island in this scenario. Perhaps the ‘open grid’ format would be a good option for a cluster of properties based around its own dedicated Distributed Energy Resources (DERs)?
Case study 4 – the islanded micro grid
Figure 12
Illustrative of something grid-privileged people forget, that some parts of the world do not have a macro grid. Also, that some may choose to live apart from it. This diagram is a gross simplification. A major challenge in this scenario is matching the DC Voltage of the source to the required voltage of the appliances. Where DC to DC voltage conversion is required a buck converter could be used.
Case study 5 – a fully-featured hybrid AC/DC system
Figure 13
This is a concept, not an actual design but it is entirely achievable, given appropriate expertise. The biggest barrier to its realisation is the lack of Appliances that can be powered directly from a DC supply!
Note the use of a 380VDC Bus to feed lower DC voltage branches.
Summary
In 2022 DC buildings are possible but significantly more challenging to deliver than AC buildings. Simply swapping a traditionally wired AC building over to a DC supply would be challenging for a variety of reasons including voltage drop, DC arcing and circuit fault protection.
In 2022 a new-build or rewire of a domestic or commercial premises could be adapted as described above to make a transition to DC viable when cost-effective solutions to the challenges are found.
Forward-thinking developers and designers can hang a 'DC future-ready' tag on their properties. The value to the owner of this is boosted by the inclusion of PV / EV / Battery Storage capability.
DC will probably have to co-exist with existing AC grid connections until the macro-grid is ready to flip to DC.
Supply follows demand, the macro-grid will only flip to DC when there are enough DC buildings to make that profitable. The forces of change that will drive the adoption of a DC macro grid include:
- The challenge of managing very large numbers of very small renewable energy sources and energy storage devices
- The need for an effective islanding capability to build resilience, and support for peer-to-peer energy trading
- The need to build the additional network capacity to charge electric vehicles and exploit vehicle-to-grid (V2G).
These things can be achieved within the existing AC macro grid - but it’s much, much harder.
Some of the technical challenges to overcome include:
- The lack of approved DC metering equipment
- The immaturity and scarcity of solid state circuit protection to substitute for MCBs
- The immaturity and scarcity of appliances which are factory-fixed to run on DC
- The creation of a macro-protocol for energy management which all stakeholders in all parts of the supply chain can adhere to
- The lack of an approved Code of Practice for DC installation. While British Standard BS 7671 incorporates the provision for systems up to 1500 VDC it is fair to say that it’s application to comparably immature DC technology is a daunting challenge for most electrical designers.
Yes, it’s a bit of a moon-shot but a DC macro-grid would be a grid fit for our 2050 goals and those goals mean everything.
So, what are we waiting for, a DC built environment isn’t going to build itself!