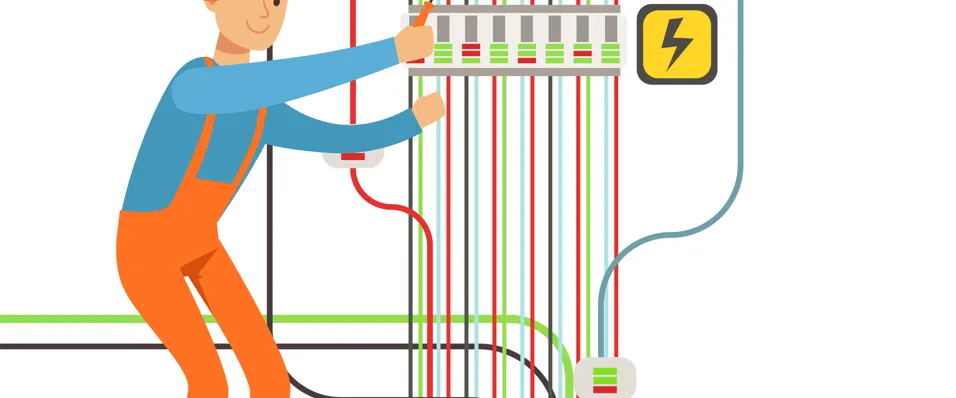
Working safely with storage: It's not business as usual
Working on a project for a remote customer in East Africa, a highly experienced electrical engineer was working on a renewable energy system which comprised solar, battery storage, a diesel generator and a grid supply. The operator, who was based in the region and trained in the UK, bypassed the batteries and solar so that the customer’s loads were still powered and so that he could work on the distribution board. Reaching into the board, he was quickly called back as his hand was just 75 mm from a bus which was live and had the potential to cause serious harm. So how did a qualified engineer who had worked on the project for six months end up so close to injury?
He had assumed that everything was safe by following standard practices from years of work on regular distribution boards. He had isolated the distribution board at the grid/generator point and disconnected the PV inverters. He had also tested for dead at the part of the board he was due to work on. Critically however, he forgot that storage introduces new risks to electrical engineers because the battery must always be considered live. This of course applies to the DC terminals of a battery, but also to the AC side of any battery inverter – unless all of the batteries are safely isolated. The grid forming inverters of some battery storage systems will often default to a live state in the absence of an external grid. This means that components that would previously be considered ‘dead’ should always be considered potentially live in a battery storage installation. In the case of this project, as soon as the distribution board had been bypassed, the battery storage inverters became grid forming and re-energised all of the busbars in the system.
Figure 1: Typical arrangement of multiple supplies. Main bus was live because battery inverters established a voltage and were not isolated at the battery AC distribution board.
Just nine months later, a similar incident occurred on the same equipment in another location which left an engineer with over twenty years’ experience with slight burns on his hand. He brushed against a busbar he assumed was dead after switching off all the diesel generators at an off-grid site. Although the external grid was disconnected and no loads were being served, the battery still formed a grid and made key elements of the distribution board live.
The risk in these two examples could have easily been mitigated by providing a correct isolation procedure for the engineer to follow. In both cases, this would have involved isolating the PV inverters or PV distribution board, tripping all of the MCCBs to isolate the battery inverters and bypassing to allow the grid and generator to meet the load. The simple procedure could have been written on a single page of paper and embellished with a series of photographs or drawings. We strongly believe that all battery systems, large or small, should be provided with some form of isolation instructions for professionals to follow.
Isolation should not be difficult and must be considered when designing the inclusion of additional sources of generation into an electrical installation. For example, single-phase installations that only have one consumer unit and one inverter could use a clearly marked 4-pole isolator. This would bring the inverter feed into two poles, and the normal supply through the other two and would isolate everything on the AC side in the installation except the feed from the inverter to the consumer unit.
UK requirements for working safely on electrical systems can be found in the HSE publication HSG85 Electricity at Work: Safe Working Practices which is free to download from the HSE website. The key points of the working dead procedure outlined in HSG85 are summarised in Figure 2.
In the case of the system in East Africa, a safe isolation procedure would of course involve disconnecting the grid, generator and PV inverters at the respective points of isolation, locking off the points of isolation, and posting relevant signage. It would also involve opening all of the breakers for the battery inverters and/or switching these off.
Isolation is not hard and neither are the adjustments that we need to safely work with battery storage systems. However, these near misses are a stark reminder of the dangers of getting it wrong when working with new technology. The risks can be mitigated through recognising that new energy technologies need to be worked on with slightly different practices. We need to avoid electricians coming to do ‘ordinary’ electrical work who are unaware of the risks and issues with EV, renewable generation and storage, and consequently putting either themselves or members of the public at risk. Ultimately, it is our aim that knowledge of EV charging equipment, electrical energy storage, Solar PV etc. becomes mainstream. Getting there will require some relatively simple additions to common safety procedures.
Figure 2: Overview of the key principles of the working dead procedure in HSG85