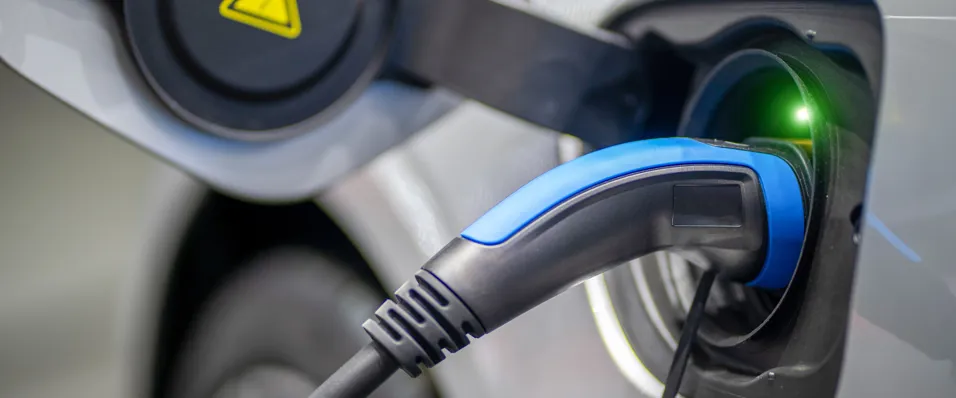
External consumer units for electric vehicles in a domestic environment
By: Craig O’Neill BEng (Hons) MIET
The pressure is on to achieve net zero. The roll out of electric vehicles, solar photovoltaics (PV) and heat pumps is set to be a big part of reaching that target, so it comes as no surprise that new challenges have been coming thick and fast for the designers and installers of electrical installations to accommodate new technologies into homes.
Renewable technologies require specific protection in order to be safe for use in line with BS 7671:2018+A2:2022. These protective devices are sometimes difficult to retrofit into existing consumer units due to the age of the existing unit or space constraints, so installers sometimes need to either replace with a larger consumer unit or install a separate consumer unit to supply electric vehicle charging equipment. If there is space inside the property adjacent to the existing consumer unit, then this is fairly straightforward and simple. However, if there is no space, then installers need to find other solutions. Some properties have external meter boxes which might be tempting to use as the location of one of these consumer units. However, the Energy Networks Association issued a statement regarding using these enclosures for this purpose:
While the meter cabinet is the customer’s, it is a space designed for the use of electricity industry apparatus only and no allowance is made for additional equipment. For safety reasons, we would not recommend that any internal wiring, including a consumer unit is installed within the cabinet.
One option which has been growing in popularity is to use an external consumer unit fitted externally adjacent to the meter cabinet.
This article looks at some of the main design considerations for such an install in a domestic environment.
What should a designer and installer consider?
External consumer units in domestic premises will need to conform to BS EN 61439 series and in particular, BS EN 61439-3 Low-voltage switchgear and controlgear assemblies. Distribution boards intended to be operated by ordinary persons (DBO).
All electrical installations need to consider the general requirements of BS 7671:2018+A2:2022 and mitigate any potential hazards at the design stage. For an external electric vehicle consumer unit, there are some specific considerations:
- Weather
- Temperature variances
- Exposure to the sun
- Corrosive or pollutive substances which would include coastal air with a high salt content
- Condensation
- Impact protection
- Protective multiple earthing (PME) supplies
- Tampering
- Rated current of circuits within the consumer unit.
Weather, temperature variances, sun exposure, and corrosive or pollutive substances
Weather, temperature variances, sun exposure, and corrosive or pollutive substances can all have a detrimental effect on electrical equipment. Electrical equipment is designed to operate within certain parameters, so any venture outside of these parameters means their reliability and/or safety cannot be assured.
Traditionally, an external consumer unit was cited in locations away from the weather such as under soffits of roofs of summer houses and out buildings, or housed in additional enclosures. This provides additional protection against the weather and prevents the user having to operate any protective devices in direct rain or snow which could be hazardous.
The weather in the UK can vary greatly and it is important for an installer to understand what that means. Driving wind and rain can penetrate even the best of seals so, using the correct entry method is essential. If attempting a rear entry from inside the property into an enclosure, ingress of moisture will almost be inevitable at some point in the future. Driving wind and rain will get past tiny gaps between any silicon used and brickwork, and then track inside either the enclosure or into the house along the cables. The temperature in the UK also varies and although these assemblies and devices are tested to the extremes (-25° C/+40° C with an average daily max of 35° C), it is important to remember that as temperatures change, so do the electrical resistances of conductors and thermally operated protective devices. In the cold they will operate slower and as temperature increases they will operate faster.
The enclosure selected will need to have suitable protection from the effects of the sun.
According to PD IEC TR 61439-0:2022 Low-voltage switchgear and controlgear assemblies – Guidance to specifying assemblies:
Solar radiation can have two impacts on assemblies and enclosures exposed to it.
- Heating effect caused by the complete spectrum of sunlight, usually referred to as solar irradiance, and
- UV radiation which has a shorter wavelength than that of visible light and can degrade synthetic material such as plastics.
These effects could make some plastics become brittle. Some plastics are formulated to be more UV stable than others.
PD IEC TR 61439-0:2022 8.5.2 mentions that the heating effect caused by the complete spectrum of sunlight is not addressed in the BS EN 61439 Low-voltage switchgear and controlgear assemblies series, except for assemblies for PV applications. Outdoor assemblies are required by the BS EN 61439 series of standards to be UV stable in temperate climates and mentions that if exposed to intense sunlight, the specifier should consult with the manufacturers on ways to increase the UV resistance.
A metallic enclosure is more susceptible to corrosion from the rain and coastal air due to higher salt content. In order to demonstrate resistance to corrosion, design verification tests are carried out in accordance with the BS EN 61439 series on representative samples or parts of the assembly to recognized standards. The tests are accelerated life tests, which use chemicals and processes to stimulate in a short time exposure of the assembly to normal atmosphere for its intended life. All assemblies are required to be resistant to a basic level of corrosion. Two levels are included for ferrous metallic parts which are severity A and severity B. Severity A is indoor equipment and the internal parts of outdoor equipment and severity B is external parts of outdoor equipment located in normal environments. PD IEC TR 61439-0:2022 mentions:
For outdoor equipment where exceptionally long service without maintenance is required, or where particularly onerous conditions prevail (for example exposure to sea spray), additional protection and/or measures can be necessary.
What is pollution degree?
According to PD IEC TR 61439-0:2022 Low-voltage switchgear and controlgear assemblies – Guidance to specifying assemblies:
It is expected that, depending on the place of installation, the air surrounding and within the assembly will contain a level of pollution. Environmental conditions at the place of installation are regarded as “macro-environment”, whereas the “micro-environment” refers to conditions within the assembly. The specifier shall state the pollution degree outside the assembly at the place where it will be installed. Depending on the protection offered by the assembly enclosure, the assembly manufacturer will then derive the pollution degree in the micro-environment inside the assembly.
The pollution degree is a classification system that relates to the amount of dry pollution and condensation present in an environment. It's important because it affects the creepage and clearance distances required to ensure the safety of a product. Here's what the pollution degrees represent:
Pollution degree 1:
No pollution or only dry, non-conductive pollution occurs. The pollution has no influence.
Pollution degree 2:
Only non-conductive pollution occurs, except that occasionally a temporary conductivity caused by condensation is to be expected.
Pollution degree 3:
Conductive pollution occurs or dry, non-conductive pollution occurs which is expected to become conductive due to condensation.
Pollution degree 4:
Continuous conductivity occurs due to conductive dust, rain or other wet conditions.
The relationship between IP rating and pollution degree is that they both provide a measure of protection for electrical equipment, but they focus on different aspects. While the IP rating system provides a measure of protection against intrusion from foreign bodies (such as dust or water) and accidental contact, the pollution degree rating focuses on the amount of dry pollution and condensation present in the environment.
In other words, the IP rating can help protect against the physical ingress of pollutants (to a certain degree), while the pollution degree rating, along with expected voltages and required voltage withstand levels, helps determine the necessary design considerations (like creepage and clearance distances) to ensure safe operation of the equipment in environments with varying levels of pollution.
However, it's important to note that neither system guarantees complete protection against all types of environmental conditions or pollutants. Therefore, both ratings should be considered when designing, selecting and using electrical equipment. It's always important to consider the specific environmental conditions that the equipment will be exposed to and ensure that it is appropriately rated or protected for those conditions.
What is creepage and clearance distances?
When discussing pollution degree, creepage and clearance are two important concepts related to the safety and function of electrical equipment.
BS EN IEC 60664-1:2020 Insulation coordination for equipment within low-voltage supply systems – Principles, requirements and tests, defines these as the following:
3.1.4 - Clearance - shortest distance in air between two conductive parts
3.1.5 - Creepage distance - shortest distance along the surface of a solid insulating material between two conductive parts.
Enclosures for outdoor and indoor installation, intended for use in locations with high humidity and temperatures varying within wide limits, shall be provided with suitable arrangements (natural ventilation, forced ventilation, internal heating, drain holes etc.) to prevent harmful condensation within the enclosure.
Degrees of protection provided by enclosures (IP code), according to the classes specified in IEC 60529, do not necessarily improve the micro-environment with regard to pollution. Different insulative materials have different effects on creepage distances.
The pollution degree of an environment affects the required creepage and clearance distances to ensure the safety of a product. For example, in some cases, the creepage distance for pollution degree 2 is 2 to 4 times longer than for pollution degree 1. This is because a higher pollution degree means a harsher environment with more dry pollution and condensation, which can affect the conductivity between conductive parts.
Condensation
Condensation is the reverse process of evaporation and occurs either when warm, moist air is cooled to its dew point, or the air becomes so saturated with moisture it can no longer hold any more moisture.
Anyone who has lived in a bedroom with single glazed windows will understand what this means. The warmer moist air on the inside of the window was cooled to its dew point when in contact with the cold surface of the glass, the glass was cooled by the colder air outside overnight and condensation formed on the inside and created a puddle on the window sill each morning.
In an electrical enclosure outside, this could be problematic. Not only would it potentially reduce the creepage and clearance distances of the devices and assembly, but, in the worst case, could pose a shock risk. If the protection of these types of external enclosure is likely to be the supplier’s overcurrent protective device, it is important to remember this type of fuse will offer very little protection from shock and is unlikely to react unless the supply conductors to the external enclosure directly make contact with each other. Designers and installers are reminded of the fundamental principles set out in Chapter 13 of BS 7671:2018+A2:2022
Eventually, any condensation forming like this inside an enclosure would increase corrosion of any metallic parts.
It is important to note that the electrical installer should not modify a consumer unit/distribution board to make it suitable for outdoors unless they intend to take on the responsibility for the conformity of the product. An appropriate product classified for use outdoors with appropriate manufacturer’s verification and declaration should be selected. The manufacturer will typically select and verify a suitable solution for the size and application of the consumer unit/distribution board with respect to condensation and pollution degree for example:
- Test the outdoor consumer unit for the external macro-environment of pollution degree 4 (for example, by thermal cycling tests, climatic durability tests) to validate that the micro-environment inside the assembly is suitable for the pollution degree and level of condensation in relation to the incorporated devices.
- Avoid fluctuations in temperature, for example, pressure relief glands validated by test as part of the consumer unit.
- Ventilate (for example, by air gland technology, vents) validated by test as part of the consumer unit.
- Install air conditioning.
- Decrease humidity.
- Keep the temperature above dew point.
PD IEC TR 61439-0:2022 explains:
Specifiers are cautioned against over-specifying their requirements; it may not lead to a more appropriate assembly for their application. More onerous requirements for one criterion usually have a negative impact on others. For example, an outdoor assembly being specified to comply with IP66 of IEC 60529, when a lower IP degree, for example IP33, will suffice, can:
– increase temperatures within the assembly due to the lack of ventilation with the effect that the insulation ages more quickly;
– increase the risk of condensation causing tracking due to there being no ventilation and therefore no air exchange with the environment outside of the assembly; and
– make the assembly larger and more expensive due to the need to manage the lack of ventilation. If special and exceptionally onerous conditions are likely to exist, these conditions should be identified by the specifier. Examples of these onerous conditions include high ultraviolet (UV) radiation applications, conditions of high particulates/pollutants, more stringent short-circuit conditions, special fault protection, special protection due to risk of fire, internal arc-faults, explosions, burns, etc.
Figure 1 below shows IP codes second numeral from PD IEC TR 61439-0:2022.
Figure 1: IP codes second numeral from PD IEC TR 61439-0:2022
These can be linked with external influence codes from BS 7671:2018+A2:2022, as seen in Figure 2, which shows external influences and equivalent IP code from BS EN 60529.
Figure 2: External influence codes from BS 7671:2018+A2:2022.
Figure 3: Example of condensation in external CU mounted directly onto a wall.
Figure 4: More extreme examples of condensation in an enclosure that had protection by an additional GRP enclosure but no additional measures in place. The condensation here caused a fault (bottom right).
Figure 5: More examples of condensation building up into corrosive puddles at the bottom of the enclosure.
Figure 6: Metallic board forming condensation inside (photo credit: Ben at Contact Electrical, Stratford upon Avon).
The BEAMA IP guide states:
Consideration should also be given to the possible effects of condensation, which can be caused by occasional temperature changes. This may be solved by ventilation, use of anticondensation heaters, climate controls or by ensuring any condensation created does not cause harm and may be allowed to drain away. Generally, an air temperature inside the enclosure, of 5 degrees above external ambient, will prevent condensation within the enclosure. Drainage holes may be sufficient to disperse the condensate, but these apertures may reduce the IP rating. However, if correctly designed, drainage holes can enhance the weatherproof capabilities of an enclosure. See sections 7 & 10.
The Guide to IP Codes can be found on the BEAMA website.
Impact protection
Avoiding any impact of an enclosure is the best way to protect the enclosure. Therefore, choosing the best location for the enclosure is critical. Low level in a high traffic location is almost certainly going to be impacted at some point. If the installation is connected via the suppliers fuse then any exposed live parts resulting from an impact could present significant shock risk. An additional enclosure to house the consumer unit would increase protection from impact.
The requirements of impact protection can be found in IEC 61439-3:2024 and BS EN 61439-3:2012 Low-voltage switchgear and controlgear assemblies - Distribution boards intended to be operated by ordinary persons (DBO).
BS EN 61439-3:2012, clause 8.2.1 Protection against mechanical impact states:
The DBO shall comply with the following IK codes according to IEC 62262:
– IK05 for a DBO for indoor use
– IK07 for a DBO for outdoor use.
Rated current of circuits within the consumer unit
PD IEC TR 61439‑0 highlights that as the IP rating increases, this can create higher temperature rises within the assembly due to the lack of ventilation. This could result in the marked/labelled rated current of protection devices being derated and these rated currents should be supplied with the consumer documentation. This is highlighted in BS 7671:2018+A2:2022 Regulation 536.4.2022:
The current rating(s) of an assembly circuit may be lower than the rated current(s) of the device(s) according to their respective device standard, when installed in the assembly; therefore, the assembly manufacturer’s ratings and instructions shall be taken into account.
It is therefore critical that the electrical installation designer ensures the consumer unit specified is supplied with the required rated current information.
PME supplies and metallic enclosures
When exporting any circuit connected to a PME supply to the outside of a property, the issue of protective earthed neutral (PEN) faults and the dangers of using a PME earthing system gets discussed. These faults are usually associated with an ageing network, but accidental damage could also cause the same outcome. At the time of writing this article, there is very little available data to decide how frequent these types of faults could occur, but the theory behind how they could occur is widely accepted throughout the industry.
The design of a PME earthing system means that there can always be a small potential difference between true earth and any exposed-conductive-parts of an exported circuit and/or extraneous-conductive-parts connected to the main earthing terminal (MET). Generally, the further away from the supply source transformer you go, the more the potential difference increases due to an increased resistance between true earth and the MET. It is therefore always a consideration for any designer to be aware of any simultaneous touch points of both exposed and extraneous-conductive-parts and true earth and, where possible, design them out to remove any hazards as IET Guidance Note 5: Protection Against Electric Shock (GN5) suggests in Section 14.4.
Figure 7: Guidance Note 5 extract regarding touch voltage potentials outside
The potential difference between true earth and any exported Circuit Protective Conductor (CPC) can be of importance when body contact resistance is low (in wet conditions or minimal clothing) and when there is good contact with true earth.
BS 7671:2018+A2:2022 Regulation 411.4.2 recommends that an additional connection to earth, by means of an electrode in accordance with chapter 54 BS 7671:2018+A2:2022, is made to the main earthing terminal. This would ensure any small potential rises between the two during normal use would become less significant, but a single electrode is unlikely to maintain safe touch voltages during an open PEN fault scenario or fault currents.
Figure 8: Table 14.1 from Guidance Note 5
Regulation 411.4.1 of BS 7671:2018+A2:2022 reminds us that the integrity of the earthing is the responsibility of the distributor.
It is theoretically possible to use an open PEN detection device (OPDD) inside an external metallic enclosure to protect the enclosure itself. There is currently no requirement within BS 7671:2018+A2:2022 to do so as Regulation 722.411.4.1 refers to the charging point and not any supply equipment. The risks however, are similar.
If a PEN fault occurred, some charging equipment may not operate. The user is likely to inspect the consumer unit which, if metallic, during a PEN fault could be live and pose a significant shock risk.
An OPDD device would involve switching the distribution circuit cpc before it connects to the casing and would need to meet the requirements of Regulation 543.3.3.101 of BS 7671:2018+A2:2022.
These devices do not currently have a product standard so the equipment would need to meet The Electrical Equipment (Safety) Regulations 2016 (as amended), The Electromagnetic Compatibility Regulations 2016 (as amended) and other relevant legislation, along with a CE, UKCA or UKNI mark and a Declaration of Conformity appended to the Electrical Installation Certificate (EIC). See Section 511 of BS 7671:2018+A2:2022 and Regulation 722.411.4.1 Note 1. It could also affect the rated current of assembly and therefore would also need to be verified by the enclosure manufacturer and work in coordination with any protective devices inside the charging equipment.
Figure 9: An open PEN detection device which operates in accordance with Regulation 543.3.3.101 of BS 7671:2018+A2:2022 and has also been third party tested by BSI labs
The most obvious method of avoiding any danger from a metallic enclosure and a PME supply would be to simply use an insulated enclosure. This would remove any contact point during normal use. BS 7671:2018+A2:2022 Regulation 421.1.201 applies within domestic premises, not external, so an insulated enclosure could be suitable. For fire considerations, it would be prudent to locate an insulated external consumer unit enclosure away from windows where people sleep, escape routes and avoid fixing to some cladding systems.
Tampering and continuity of service
All outdoor, accessible switchgear is vulnerable to tampering. If the enclosure is for an electric vehicle charger and someone decided to turn it off for you, then you may wake up to a flat battery. This could be significant for times of emergency or important call outs such as lifeguards, fire service etc.
Other considerations
As time moves on, electricians will be conducting Electrical Installation Condition Reports (EICRs) and coming across enclosures like this and it is important to know which ones have been verified by the manufacturer and which ones someone have just been put together themselves from an empty enclosure and devices. This is important as the rated current of assembly verified by the manufacturer may be less than the device marked ratings. Different devices may have different heating effects. It is important that a manufacturer has verified the assembly to BS EN 61439-3.
Summary
Key points:
- Domestic external consumer units need to conform to BS EN 61439-3 and other relevant parts.
- Direct sunlight will heat the enclosure and may not have been verified by the manufacturer for that environment.
- It is the responsibility of the manufacturer to interpret appropriate product standards and important to consult the manufacturer regarding any modifications required of the enclosure.
- Remember the installation basics of maintaining the declared IP rating, such as bottom entry appropriate glands, level and flat to surface fixing, secure fixings etc.
- A supplier’s cutout offers little protection against electric shock, so condensation and impact are important considerations.
- Regulation 421.1.201 of BS 7671:2018+A2:2022 applies within a dwelling not externally, so there is no requirement for the enclosure to be metallic.
- An additional enclosure would help protect against impact, direct weather and provide a higher degree of safety for users to operate protective devices in wet conditions.
- Many engineers would regard this method of installation as a ‘last resort’ design option.
Thank you to the following people for their invaluable comments and advice when writing this article:
- BEAMA
- Gary Parker
- Michael Peace
- Leon Markwell
Special thank you to Susannah Girt.
Permission to reproduce extracts from British Standards is granted by BSI Standards Limited (BSI). No other use of this material is permitted.