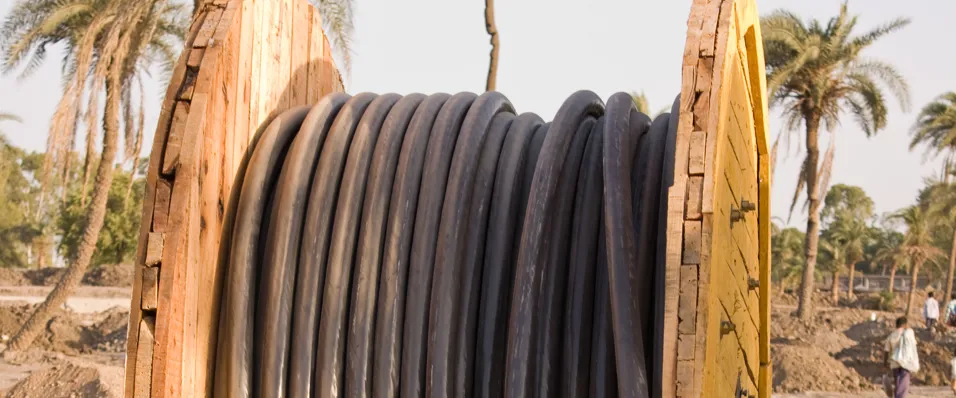
Thermoplastic (PVC) or Thermosetting (XLPE) SWA cable?
A question that arises periodically on the IET Engineering Communities forum concerns the different types of steel wired armoured (SWA) cables and the associated current-carrying capacity.
What are the different types of SWA cable?
The two types of SWA cable referred to in Appendix 4 of BS 7671:2018+A2:2022 are thermoplastic insulation, which is polyvinyl chloride (PVC), and thermosetting insulation, which is cross-linked polyethene (XLPE).
PVC insulated and PVC sheathed SWA cables were manufactured to BS 6346 Electric cables. PVC insulated, armoured cables for voltages of 600/1000 V and 1900/3300 V. The standard was originally published in 1969. Prior to this, PVC SWA cables were manufactured to BS 3346:1961 Armoured PVC-insulated cables.
However, BS 6346, the standard for PVC cables, was withdrawn in 2011. SWA cables are generally only manufactured with XLPE insulation to either BS 5467, BS 6724 or BS 7846, as listed in Table 4A3 in BS 7671.
BS 5467 Electric cables. Thermosetting insulated, armoured cables of rated voltages of 600/1 000 V and 1 900/3 300 V for fixed installations.
BS 6724 Electric cables. Thermosetting insulated, armoured cables of rated voltages of 600/1 000 V and 1 900/3 300 V for fixed installations, having low emission of smoke and corrosive gases when affected by fire, if a low smoke zero halogen (LSZH) sheath is required.
BS 7846 Electric cables. Thermosetting insulated, armoured, fire-resistant cables of rated voltage 600/1 000 V for fixed installations, having low emission of smoke and corrosive gases when affected by fire, for fire resistant applications.
PVC insulated and sheathed SWA cables may be still manufactured to the withdrawn standard in small quantities, primarily used for traffic signals. The vast majority of SWA cables though will be XLPE insulated, and have been for the last twenty years.
It is also worth pointing out that aluminium wire armoured (AWA) cables also exist, typically used for single core conductors due to their non-ferrous properties.
When did thermosetting XLPE SWA cables first appear in the IEE Wiring Regulations?
The British Standard for thermosetting cables, BS 5467, was originally published in 1977. The first appearance of thermosetting SWA cables was in the Fifteenth Edition of the IEE Wiring Regulations in 1981, as shown in Table 9E1 (Figure 1). Note that the conductor cross sectional area starts from 16 mm². This was because at the time, cable manufacturers only had the machinery to make the change for the larger sizes, so it was agreed to test the water with the market first before they all invested in new machinery to cover the smaller sizes, a kind of ‘soft launch’. The benefit in uplift from current ratings is not as significant on the smaller sizes, and equipment that required the smaller size conductors was less likely to capable of operating at the higher 90 °C.
In the Sixteenth Edition of the IEE Wiring Regulations in 1991, the table was relabelled Table 4E4A as we know it today and the table included information for conductor sizes from 1.5 mm² - 400 mm².
Figure 1: Extract from Fifteenth Edition of the IEE Wiring Regulations 1981
The construction of an SWA cable
Figure 2 illustrates a typical SWA cable construction and its constituent parts. When we refer to a particular type of cable, such as PVC or XLPE, it is the material used for the insulation which is referred to. Whilst the insulation material used is XLPE, the bedding and sheath are made from PVC. The table below indicates the typical construction and materials used in an XLPE armoured cable.
Conductor | Copper |
Insulation | XLPE |
Bedding | PVC |
Armour | SWA |
Sheath | PVC |
Figure 2: Cable construction
What are the advantages and disadvantages of thermosetting insulation?
Besides having a higher temperature rating, thermosetting insulation offers higher insulation resistance values, increased mechanical protection and resistance to chemical corrosion and water. There are also disadvantages to thermosetting insulation, since it is more difficult to strip than thermoplastic insulation.
When it comes to recycling, usually only the metals, the copper conductors and/or the steel or aluminium armouring is considered due to the value of these metals. However, PVC materials can be recycled and made into something else, whereas XLPE cannot be melted as it is cross-linked.
Under fire conditions PVC cables create toxic fumes and large quantities of smoke, potentially making escape more difficult. PVC material is used for the bedding and sheath components of XLPE cables. If the cables are installed indoors and a low smoke zero halogen (LSZH) solution is required, LSZH SWA cables manufactured to BS 6274 should be specified, as they do not contain PVC or any other halogenated material.
Does thermosetting insulated SWA cable have higher current carrying capacity than thermoplastic insulated SWA cable?
Appendix 4 of BS 7671:2018+A2:2022 includes the current-carrying capacities for SWA cables. Table 4D4A is for multicore armoured thermoplastic cables and Table 4E4A is for multicore armoured thermosetting cables, as seen in Figure 3 and Figure 4.
When making a direct comparison of current-carrying capacity for thermoplastic and thermosetting cables in Table 4D4A and 4E4A, the current-carrying capacity of thermosetting cables is higher when compared with the equivalent thermoplastic cable. The increased current-carrying capacity is due to a higher conductor operating temperature of 90 °C. It is important to read the notes next to table 4E4A, as they provide guidance regarding compatibility.
Figure 3: Table 4D4A of BS 7671:2018+A2:2022
Figure 4: Table 4E4A of BS 7671:2018+A2:2022
What is compatibility?
Regulation 512.1.5 of BS 7671:2018+A2:2022 sets out the requirements for compatibility as shown in Figure 5. The intention of this Regulation is to ensure that every item of equipment will not cause harmful effects to other equipment with regards to EMC and temperature ratings.
Figure 5: Regulation 512.1.5 of BS 7671:2018+A2:2022
It is stated that:
”Switchgear, protective devices, accessories and other types of equipment shall not be connected to conductors intended to operate at a temperature exceeding 70 °C at the equipment in normal service unless the equipment manufacturer has confirmed that the equipment is suitable for such conditions”.
This is also reinforced in Regulation 523.1 and footnote b in Table 52.1 of BS 7671:2018+A2:2022.
Figure 6: Table 52.1 BS 7671:2018+A2:2022
Which table do I use for current-carrying capacity for thermosetting SWA cables?
As SWA cables are primarily manufactured using thermosetting insulation, you would be forgiven for thinking that the correct table to use would be Table 4E3A or Table 4E4A of BS 7671:2018+A2:2022, as these are the tables for current-carrying capacities for thermosetting cables. However, these ratings are for conductor operating temperatures of 90 °C.
If manufacturers do not confirm their equipment is suitable to operate at a temperature in excess of 70 °C, the tabulated current-carrying capacities in Table 4E3A or Table 4E4A of BS 7671:2018+A2:2022 cannot be used.
Note 3 of Regulation 512.1.5 of BS 7671:2018+A2:2022 states that, where the current rating is based on 70 °C, the tables for thermoplastic cables should be referenced instead, as shown in Figure 3.
Most electrical design software packages have an option to use thermoplastic, thermosetting or thermosetting limited to ‘run at 70 °C’, in which case, the current carrying capacities and voltage drop values are taken from Table 4D3A, 4D4A. 4D3B and 4D4B of BS 7671:2018+A2:2022 for thermoplastic cables.
Which ‘k’ value do I use for current-carrying capacity for thermosetting insulation?
The limiting factor of 70 °C conductor operating temperature for selection of cables for current carrying capacity is related to deterioration of equipment or accessories caused by constant loads of long duration. When carrying out fault current calculations, the value of k, for calculation of the effects of fault current, may be taken to correspond to the final temperature for thermosetting insulation.
For example, as shown in Table 43.1 of BS 7671:2018+A2:2022 below, the final temperature for 90 °C thermosetting insulation is 250 °C (k =143), compared with 70 °C thermoplastic insulation which has a final temperature of 160 °C (k =115) for conductors < 300 mm² and 140 °C (k = 103) for conductors > 300 mm². This could provide advantages for thermosetting insulation over thermoplastic insulation as higher fault currents can be achieved, but a key constraint is that the thermosetting insulation is not in contact or mixed with thermoplastic insulated cables.
Examples of instances where a reduced CSA could be selected when compared with that of a thermoplastic insulated cable include:
- When omission of overload protection (for a fixed load) is utilised, and using a device for fault protection only
- When carrying out energy let through calculations for a protective device like a BS EN 60947-2 MCCB
- When using an RCD for fault protection
Table 43.1 of BS 7671:2018+A2:2022
Why is the temperature rating of switchgear, protective devices, accessories and other types of equipment limited to 70°C?
The IEC 61439 series of standards sets out the requirements for low-voltage switchgear and controlgear assemblies. PD IEC TR 61439‑0:2022 Guidance to specifying assemblies states: “The temperature performance of assemblies in accordance with the IEC 61439 series assumes the temperature of the conductors outside the assembly, in normal service, is a maximum of 70 °C.”
In conclusion, assemblies to the IEC 61439 series are included in Regulation 512.1.5 of BS 7671:2018+A2:2022. Switchgear, protective devices, accessories and other types of equipment shall not be connected to conductors intended to operate at a temperature exceeding 70 °C at the equipment in normal service unless the equipment manufacturer has confirmed that the equipment is suitable for such conditions.
Summary
Most SWA cables are thermosetting insulated. Thermosetting cables are capable of operating at conductor operating temperatures of 90 °C, but it should be verified with the equipment manufacturer that this is safe. Unless this is confirmed, the current carrying capacities identified in Table 4D3A or Table 4D4A of BS 7671:2018+A2:2022 for thermoplastic SWA cables should be used.
Acknowledgments
I would like to extend thanks to Joe Cannon for suggesting the idea for the article and his valuable contributions. I met Joe at the Elex show in Bolton this year, where we originally discussed the idea.
I would also like to extend sincere thanks to the following individuals and organisations for contributing their technical expertise:
- The British Cables Association (BCA)
- Leon Markwell
- Mark Coles
- Paul Sayer
- Paul Skyrme
Further reading
BS 7671:2018+A2:2022 Requirements for Electrical Installations.
PD IEC TR 61439‑0:2022 Low-voltage switchgear and controlgear assemblies- Part 0: Guidance to specifying assemblies
BS 5467 Electric cables. Thermosetting insulated, armoured cables of rated voltages of 600/1 000 V and 1 900/3 300 V for fixed installations.
BS 6724 Electric cables. Thermosetting insulated, armoured cables of rated voltages of 600/1 000 V and 1 900/3 300 V for fixed installations, having low emission of smoke and corrosive gases when affected by fire, if a low smoke zero halogen (LSZH) sheath is required.
BS 7846 Electric cables. Thermosetting insulated, armoured, fire-resistant cables of rated voltage 600/1 000 V for fixed installations, having low emission of smoke and corrosive gases when affected by fire, for fire resistant applications.