
Mythbuster #5 – Will any old terminal block do?
Nearly every electrical installation will need to join conductors of different parts of a circuit, typically by using a connector of some type, such as a terminal block, DIN rail terminal, junction box or similar. A common type of connector is the ‘choc block’ terminal strip, but more recently connectors using spring clamps to hold wires firmly are becoming common. While no competent electrician would wrap wires together and cover them with insulating tape (though it does happen!), is it actually acceptable to use any old terminal for an electrical connection?
As befits a Standard with such a pedigree as BS 7671, there are requirements for electrical connections, just as there were in the 1st Edition, back in 1882. As it happens, back then the jointing of conductors was an exercise in wrapping wires together in a rather elegant fashion, but of course, technology has moved on since and Regulation group 526 of BS 7671:2018 is where the relevant requirements are now detailed. While there is the obvious need to ensure that the connections between conductors are electrically and mechanically sound (Regulation 526.1), there are a few requirements that are often overlooked.
Regulation 526.2 requires that the selection of the means of connection should take into account the following:
i. the material of the conductor and its insulation
ii. the number and shape of the wires forming the conductor
iii. the cross-sectional area of the conductor
iv. the number of conductors to be connected together
v. the temperature attained at the terminals in normal service such that the effectiveness of the insulation of the conductors connected to them is not impaired
vi. the provision of adequate locking arrangements in situations subject to vibration or thermal cycling. Where a soldered connection is used, the design shall take account of creep, mechanical stress and temperature rise under fault conditions.
The materials used for the conductor and terminal are quite an important consideration, which is often overlooked. Where dissimilar metals are used, galvanic corrosion can occur giving rise to high impedances. This can not only impair the effectiveness of protection of a circuit but can cause issues around the requirements for electromagnetic compatibility (Section 444), as poor joints may exhibit higher impedances at higher frequencies. Such poor joints can even cause interference if conductors are part of circuits where high frequencies are present, due to the ‘rusty bolt effect’, as well as creating noise voltages to which sensitive circuits may be susceptible.[1]
The thermal aspects are another consideration in selecting an appropriate terminal. Firstly, Regulation 526.4 requires that the means of connection (and its insulation) must be rated for the maximum operating temperature of the conductor, the values of which are given for different cables in the appropriate tables in Appendix 4. Secondly, the insulation around the connection should be non-flame propagating, and Regulation 526.5 requires terminations and joints to be within a suitable accessory or enclosure. This is important for reasons of mechanical protection, as well as for electrical insulation of the connections. When the inner cores of a cable are jointed (for example, in a terminal or spliced), the protection afforded by the sheath has been removed and needs to be replaced to provide electrical and mechanical protection. It is, therefore, possible to use maintenance-free joints that will not require access for inspecting or maintenance, but the joint(s) should be contained in a suitable, mechanically robust and suitably insulated enclosure – in other words, not PVC tape!
Regulation 526.3 is perhaps better known – it’s the regulation that states that connections should be accessible for inspection, testing and maintenance, save for some exceptions, such as buried, soldered or welded joints. An exception is also made for connections made by an ‘appropriate compression tool’, which may, for example, include crimped splices. It’s very tempting to use pliers to crimp many joints, but it is important to ensure that the correct pressure is applied uniformly, so the use of a proper ratchet crimp tool is appropriate to ensure a reliable maintenance-free joint.
An often raised question concerns what to do with the termination of finely stranded conductors, such as in flexible cables in light fittings or plugs/sockets. Regulation 526.9 deals with these and notes that in order to avoid separation or spreading of fine strands, ‘suitable terminals shall be used or the conductor ends shall be suitably treated’. A suitable terminal could be a rising-clamp style terminal that compresses the conductor against flat surfaces, or a push-fit spring-loaded clamp that holds all the strands tight.
A ‘suitable treatment’ for a stranded conductor is commonly the bootlace ferrule, a funnel-mouthed thin-walled metal tube that is crimped over the conductor to hold the strands in place. These are a useful method of ensuring a good joint in connections relying on screws to clamp the conductor in place, such as in a ceiling rose. Again, the use of an appropriate crimp tool is required, as the ferrule should be crimped over the conductor before insertion in the terminal; the pressure from the screw should not be used to ‘crimp’ the tube.
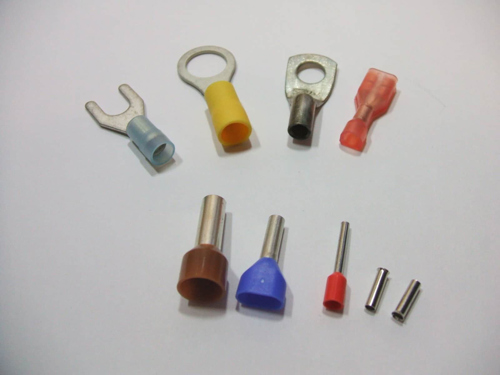
In the old days, soldering (tinning) of the whole conductor end of stranded wires was common. Nowadays, this is not permitted if screw terminals are used, because the solder can ‘cold flow’ around the screw head, resulting, over time, in a loose joint.
Interestingly, there are Standards for such connections. BS EN 60947-7-1 Low-voltage switchgear and controlgear. Ancillary equipment. Terminal blocks for copper conductors has requirements for the construction of terminals, while BS EN 60998 Connecting devices for low-voltage circuits for household and similar purposes covers connection units such as the traditional round lighting junction blocks.
There are other related Standards, such as BS 5733 General requirements for electrical accessories, which has requirements for maintenance-free connections (for example, spring-loaded terminals) and BS EN 60670-22, which is the Standard for connection boxes required where two or more circuits are terminated in a single junction (Regulation 521.8.3).
Product Standards are there for a reason, namely, to ensure that products will perform as expected and, as required, afford an appropriate level of safety. The lack of application of Standards to choc-block terminal strips, for example, is illustrated by the following comment on the IET Forum:
“I've had problems with the quality of 5A connectors where the tunnel splits as you tighten the screw.”
A terminal made to a suitable Standard should not fail when tightened appropriately, but if there is no Standard for aspects such as the material metallurgy, the thickness of the wall or other dimensions, then it is not unexpected that the more unscrupulous manufacturers will save costs by using less material, with the results that the forum member has found.
For these reasons, it is important to ensure that wiring and accessories are demonstrably safe and compliance with Standards is the most established method of proving as much. In the Common Rules for selection and erection of equipment (Chapter 51), Regulation 511.1 requires that:
Every item of equipment shall comply with the relevant requirements of the applicable British or Harmonized Standard, appropriate to the intended use of the equipment. The edition of the standard shall be the current edition, with those amendments pertaining at a date to be agreed by the parties to the contract concerned (see Appendix 1).
Alternatively, if equipment complying with a foreign national standard based on an IEC Standard is to be used, the designer or other person responsible for specifying the installation shall verify that any differences between that standard and the corresponding British or Harmonized Standard will not result in a lesser degree of safety than that afforded by compliance with the British or Harmonized Standard. Such use shall be recorded on the appropriate electrical certification specified in Part 6.
Perhaps the last word should go to Regulation 133.1.3 – one of the Fundamental Principles contained in Chapter 13 which is summarised as follows:
Where equipment to be used is not [covered by a British or Harmonized Standard] or is to be used outside the scope of its standard, the designer or other person responsible for specifying the installation shall confirm that the equipment provides at least the same degree of safety as that afforded by compliance.
So, will any old joint do? Clearly not – choose your connectors wisely!
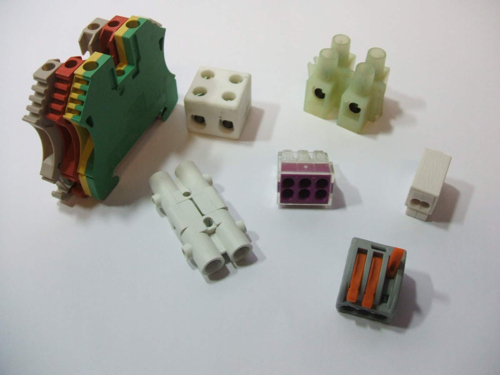
[1] See https://en.wikipedia.org/wiki/Rusty_bolt_effect for a brief description. Requirements for protective bonding co-ordination for electromagnetic interference (EMI) are contained in BS EN 50310:2016 Telecommunications bonding networks for buildings and other structures.