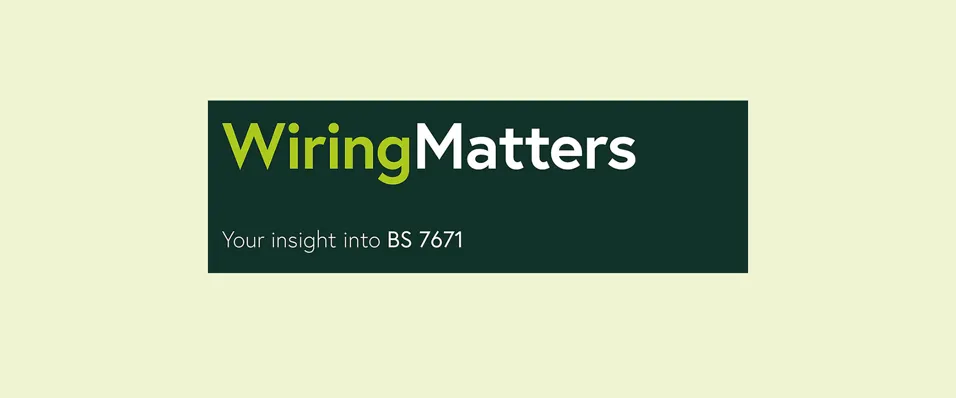
Statutory and non-statutory documents applicable to the electrical industry
If so, a time will come – if it hasn’t already – when you will need to know how to stay on the right side of the law. So, do you know the difference between which legislation has to be complied with and which documentation you can rely on to help comply with it? If not, Gary Gundry, electrical safety specialist, trainer and technical consultant, is here to help.
What to comply with and where to reach for guidance are two questions that are often asked of candidates who have taken (or are considering taking) the industry recognised exam that covers ‘initial’ or ‘periodic’ inspection and testing of electrical installations, or the in-service inspection and testing of electrical equipment. So, if you have ever wondered if you got the question right – or you need to know now which documents are ‘statutory’ or ‘non-statutory’ – this article is sure to help save you some research time and/or headaches!
Statutory documentation
In Great Britain, the ‘law’ is the generic term for any legal rule or regulation enforced by government to regulate behaviour or activities in society and is made up of either ‘primary’ or ‘secondary’ legislation.
Primary legislation is the general term that embraces main laws passed by government and includes Acts of Parliament, Acts of pre-UK Parliaments, and Acts of the Scottish Parliament etc. The aforementioned are usually used to create new laws or to introduce changes to existing ones. However, the actual process of passing an Act through Parliament can be complex and is often timely because each proposed ‘law’ starts life as a ‘Bill’, which, irrespective of its type (as in ‘public’ or ‘private’ Bill etc.) has to be debated and approved in both the House of Commons and the House of Lords. Then, once agreed in both Houses, it has to be formally agreed to by the reigning monarch (known as Royal Assent). When it comes into force, as an Act, either immediately, on a specific future date, or in stages, it is then enforceable in all areas of Great Britain, where applicable.
An example of the above is how the Housing and Planning Bill, proposed in 2015, eventually became the Housing and Planning Act in 2016. This Act, for instance, includes a small section on electrical safety that includes a provision for the Secretary of State, should he or she so wish, to impose certain duties on private landlords of residential premises in England. In consequence, such duties may include having to have a qualified person check that the electrical safety standards of the rented dwelling are met on an ongoing basis and the landlord to obtain the appropriate documentation (i.e. an Electrical Installation Certificate or an Electrical Installation Condition Report, as applicable) from the qualified person. The landlord may also be required to give a copy of that certificate or report to the tenant or prospective tenant.
Important Bills for the electrical industry
Over the next few years, a number of Bills are planned to be put before government, the first of which will be the Repeal Bill, the central piece of Brexit legislation. Two others worthy of mention, associated to the electrical industry, are:
- the Automated and Electric Vehicles Bill, which will allow, amongst other things, government to install electric vehicle charging points at motorway service areas and large fuel retailers, and to require a set of common technical and operational standards, all of which will ensure charging points are convenient to access and work seamlessly up and down the country, as these provisions will apply to England, Wales and Scotland.
- the Smart Meter Bill, announced in the Queen’s speech in June 2017, will see the smart meter rollout program be softened by means of a five-year extension, to allow for changes to regulations to ensure it is delivered effectively. In addition, every household and business is likely to be ‘offered’ such a device by 2020, instead of actually having one installed.
As you can see, a considerable amount of time and effort has to go into the creation and/or amendment of an Act of Parliament. So, to ensure longevity and prevent any rework in the form of amendments etc., each Act essentially contains only a broad framework of what is required in law. Therein, within the main body of each Act, powers are often bestowed on ministers to make more detailed ‘Orders’, ‘Rules’ or ‘Regulations’, to include all of the necessary detail that is considered too complex to include in the body of an Act. These documents, known as Statutory Instruments (SIs), are sometimes referred to as secondary level legislation (or ‘delegated’ or ‘subordinate’ legislation). They allow for the provisions of an Act of Parliament to be subsequently brought into force or altered without Parliament having to pass a new Act (i.e. primary legislation).
Examples of statutory documents
The statutory documents considered most applicable to electrical installations and/or the in-service inspection and testing of electrical equipment include:
- The Health and Safety at Work etc. Act 1974 (HASAWA)
- The Management of Health and Safety at Work Regulations 1999
- The Electricity at Work Regulations (EWR) 1989
- The Provision and Use of Work Equipment Regulations 1998 (PUWER).
The Health and Safety at Work etc. Act 1974
The Health and Safety at Work etc. Act 1974 (sometimes referred to as HSW Act or HASAWA) is a primary piece of legislation that covers occupational health and safety in Great Britain and is enforced by the Health and Safety Executive (HSE), local authorities, and other enforcing authorities relevant to the working environment.
It sets out the general duties that employers have towards employees and members of the public, and employees have to themselves and to each other. However, these duties are often qualified in the HASAWA by the phrase ‘so far as is reasonably practicable’. So, this means that (safety) measures do not have to be taken to avoid or reduce risk if it is technically impossible to do or the time, effort and/or cost of a protective measure would be grossly disproportionate to the risk. Good management and a common-sense approach, to look at what the risks might be and taking sensible measures to address them, will go a long way to meeting this requirement.
Essentially, the HASAWA places responsibility on those who create any risk to manage that risk, and this applies whether the risk-maker is an employer, self-employed or a supplier or manufacturer of items or substances for use at work. And, depending on their status, each risk-maker may have a range of duties that he or she can (and sometimes will have to) implement in order to manage the risk(s). Without doubt, workforce involvement and, in particular, the help of health and safety representatives will often make a valid contribution to raising standards of health, safety and welfare in the workplace.
The full text of this Act can be viewed or downloaded free of charge from legislation.gov.uk.
The Management of Health and Safety at Work Regulations 1999
The intention of the Management of Health and Safety at Work Regulations 1999 is to make more explicit what employers are required to do in order to manage health and safety under the Health and Safety at Work Act. Like the HASAWA, these Regulations apply to every work activity.
The main requirement of these regulations is on employers to carry out a risk assessment. And, where employers have five or more employees, there is a need to record the significant findings of the risk assessment.
The HSE would ideally like risk assessments in simple workplaces, such as a typical office, to be as straightforward as possible and only be complicated where they have to deal with serious hazards such as those in a chemical plant, laboratory or in something as large as a nuclear power station.
The full text of these regulations can be viewed or downloaded free of charge from legislation.gov.uk.
The Provision and Use of Work Equipment Regulations 1998
These regulations, often abbreviated to PUWER, require work equipment to be constructed in such a way that it is suitable for the purpose for which it is to be used. Once again, the employer (which can also be a self-employed person) is responsible for these arrangements.
The regulations deal with the work equipment and machinery used every day in workplaces and aims to keep people safe wherever such equipment and machinery is used at work.
Put simply, the aim of the PUWER is to make safer the working lives of everyone who operates, uses or comes into contact with machinery and equipment. This includes employers, employees, contractors, suppliers, and anyone else who might use or have access to machinery and equipment within the workplace. To summarise, the aim of the regulations is to ensure that all equipment is:
- suitable for its intended use.
- safe for use, maintained in a safe condition and inspected regularly to ensure that it is correctly installed and does not subsequently deteriorate.
- used only by people who have received adequate information, instruction and training to do so.
- accompanied by suitable health and safety measures, such as protective devices and controls. These will normally include emergency stop devices, adequate means of isolation from sources of energy, clearly visible markings and warning devices.
- used in accordance with specific requirements for mobile work equipment and power presses.
These regulations do not only apply to large businesses. If you operate or control work equipment, or you’re self-employed operating for profit or not, then you have a legal obligation to follow them as well.
Some work equipment is subject to other health and safety legislation in addition to PUWER. For example, lifting equipment must also meet the requirements of Lifting Operations and Lifting Equipment Regulations 1998 (LOLER), and personal protective equipment must meet the PPE Regulations 1992.
PUWER applies to all workplaces and work situations where HASAWA applies and covers the whole of Great Britain, and beyond to specified offshore areas and activities (such as those covering oil rigs and gas supply platforms).
The full text of these regulations can be viewed or downloaded free of charge from legislation.gov.uk.
The Electricity at Work Regulations (EWR) 1989
The purpose of these regulations is for precautions to be taken against the risk of death or personal injury from electricity in work activities.
Whilst these regulations cover many aspects of electrical safety, duties in some of the regulations are subject to the qualifying term ‘reasonably practicable’ and where this qualifying term is absent from a regulation it is said to be ‘absolute’. In the case of the latter, this essentially means that no matter how much time, cost and effort is involved, the requirement of that regulation has to be met. This applies to, for example, ‘electrical connections’, which have to be mechanically and electrically sound – all of the time. All other regulations have a relaxation on the aforementioned requirement as they contain the phrase ‘so far as is reasonably practicable’. This generally means everything ‘reasonably practicable’ has to be done to protect people from harm, which means balancing the level of risk against the measures needed to control the real risk in terms of money, time or trouble (similar to the HASAWA). However, no action need be taken if it would be grossly disproportionate to the level of risk.
The full text of these regulations can be viewed or downloaded free of charge from legislation.gov.uk.
Non-statutory documents associated with the electrical industry
The term ‘non-statutory’ was originally associated with common law and/or based on customs, precedents or previous court decisions. But, in the world of electrical installations it has become common practice to use this term to describe the most reliable and informative industry reference material, such as Codes of Practice (COP), British Standards (such as BS 7671) and even Best Practice Guides, to name but a few. Here are some of the main ones, together with a brief description:
BS 7671: 2008+A3:2015
Despite having the word ‘regulations’ printed on the front cover, its full and proper title is BS 7671 Requirements for electrical installations.
This British Standard sets the standards for electrical installations in the UK and many other countries and is the authority on electrical installation. So, all those concerned with the design, installation and maintenance of electrical wiring in buildings, including electricians, electrical contractors, consultants, local authorities, surveyors and architects, should have a good understanding of its contents and intentions.
As well as being essential for professional engineers and the like, this publication is also a must-have for students at university and further education colleges.
It is co-published by the Institution of Engineering and Technology (IET) and British Standards Institution (BSI).
Following the guidance set out in BS 7671 is likely to ensure that electrical installation work meets the requirements of the Electricity at Work Regulations 1989.
IET’s On-Site Guide
The On-Site Guide is one of a number of publications offered by the IET to provide guidance on certain aspects of BS 7671.
Its scope generally follows that of BS 7671 and also includes some material that is not included in BS 7671. It provides the background to the intentions of BS 7671 and gives other sources of information as well. It does not, however, ensure compliance with BS 7671, as it is a simple guide to the requirements of BS 7671. So, electrical installers and/or designer should therefore always consult BS 7671 to satisfy themselves of compliance.
It cannot be guaranteed that BS 7671 complies with all relevant statutory regulations. It is, therefore, essential to establish which statutory and other appropriate regulations apply and to install accordingly. For example, an installation in licensed premises may have requirements that differ from, or are additional to, BS 7671 and these must take precedence.
IET’s Guidance Notes (1-8)
These eight publications are designed to provide more detailed guidance about specific areas on BS 7671. In order, each publication covers:
Guidance Note 1: Selection and erection
Guidance Note 2: Isolation and switching
Guidance Note 3: Inspection and testing
Guidance Note 4: Protection against fire
Guidance Note 5: Protection against electric shock
Guidance Note 6: Protection against overcurrent
Guidance Note 7: Special locations
Guidance Note 8: Earthing and bonding
NICEIC’s guidance – Inspection, Testing and Certification
The aim of this publication is to promote best practice by providing electrical contractors and others with practical advice, guidance and answers to a number of questions that commonly arise during the inspection and testing of electrical installation work, or during the preparation of the associated certificates and reports.
It essentially complements Part 7 Inspection and testing of BS 7671 and the information and advice provided in other authoritative publications such as IET’s Guidance Note 3. It covers the general requirements relating to the inspection and testing of electrical installations forming part of TN-C-S, TN-S and TT systems in the UK, but not specialised electrical installations such as fire alarm and emergency lighting systems, or installations in hazardous areas.
The book also assumes that all persons undertaking such work already have acquired the necessary knowledge, understanding and skill, and are properly equipped, to undertake such work without putting themselves and others at risk. It is therefore not intended to be an instruction booklet for untrained and inexperienced persons.
GS 38 (Fourth edition) 2015 – HSE guidance document
This guidance document made available by the HSE is aimed at people who use electrical test equipment on low voltage electrical systems and equipment, and is principally aimed at electricians, electrical contractors, test supervisors, technicians, managers or appliance retailers/repairers, and to trades where electrical testing is not their primary activity (such as plumbers and gas engineers).
The guidance within GS 38 focuses on the correct selection and use of:
- test probes, leads, lamps, voltage detecting devices, and
- measuring equipment
for circuits with rated voltages not exceeding 1000 V AC.
In line with the Electricity at Work Regulations 1989, those in control of all or part of an electrical system are required to ensure that it is safe to use and it is maintained in a safe condition.
The full text of GS38 can be viewed or downloaded free of charge from www.hse.gov.uk.