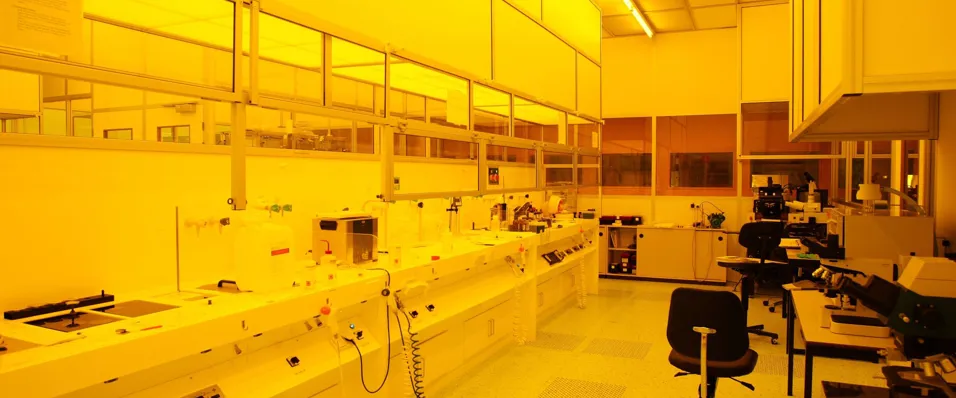
The arc flash hazard and UK guidance
There have been recent calls on social media platforms for the Institution of Engineering and Technology (IET) and the Health and Safety Executive (HSE) in the UK to do more to address the issue of arc flash* (electrical flashover) when protecting electrical workers.
I’ve written this article to highlight what the UK legislation on electrical safety says about the subject and what credible information is out there right now to help duty holders** to comply with the law. The views expressed are my own and are not intended to represent the IET or other organizations mentioned.
*“Arc flash is a non-contact short circuit between an energised conductor such as a busbar or cable with another conductor or an earthed surface. Put simply, arc flash is precipitated by insulation breakdown and very often, the insulation in question on low voltage systems is air.” IET Factfile - Arc flash risk management.
**As defined in Memorandum of Guidance on the Electricity at Work Regulations: HSR25 (Health and Safety Guidance), “Regulation 3, Persons on whom duties are imposed by these Regulations”.
Firstly, it is unlikely that the HSE will be publishing a specific guidance document on arc flash in the near future, although it is clear from the current HSE guidance, that the arc flash hazard must be treated very seriously. Whilst not a spokesman for the HSE in any way, I am aware that they have been willing to add to the debate of arc flash risk management and I have shared platforms with HSE representatives since 2007. I’m the convenor for the IEC TC 78 Working Group 15 Arc Flash Protection and on my group, there are 44 experts from 19 countries around the world. Only one National Committee has an HSE government regulator on this working group and that is Great Britain (British Standards Institute). The help given from the same regulator in publishing the IET Arc flash risk management Factfile has also been gratefully received.
The legislation in the UK is primarily risk based, goal setting and non-prescriptive. The strategic approach of the HSE is that of simplification, meaning that duty holders are expected to manage the risks that they create, as they are best placed to control them. They are expected to do so in a proportionate and practicable way, meaning that a one size fits all approach to arc flash risk management will not meet the needs of every industry or environment.
IET Arc flash risk management Factfile
In the UK, it can be said, and with certainty, that the greatest prevalence of arc flash injuries is among electrically qualified workers. Often, those working with or near electricity do not appreciate the risk of serious injury or damage to equipment that can arise from arcing. It is important therefore, that this group of workers are made aware of the hazard and the safeguards. The IET Engineering Safety Policy Panel, of which I was the Vice Chair, created a Factfile in 2021 called Arc flash risk management. The Arc Flash Working Group consisted of senior electrical engineers including an HM Principal Specialist Inspector (Electrical Engineering) and Professional Lead at the Office for Nuclear Regulation.
The Factfile is free to all and can be obtained from the IET.
Figure 1: The IET Arc flash risk management Factfile
The IET Factfile provides a helpful appreciation of the principles of arc flash risk assessments. It is an awareness document, ideally leading those who require an arc flash assessment to seek competent advice. It seeks to set out the key principles of arc flash risk management using a risk-based approach. It is aimed at persons (duty holders) with responsibility for the management of safety in the control and implementation of work on electrical power equipment.
The document describes an approach, based on a hierarchy of risk control measures. It adopts a holistic risk management methodology using the 4Ps of Predict, Prevent, Process and Protect to ensure that arc flash hazards are systematically identified, analyzed, and prevented from causing harm.
Removal of the hazard through working only on or near equipment that is made dead and suitably isolated should always be the first-choice risk reduction measure. However, other prevention measures are identified that fall into the categories of automatic disconnection of supply, equipment design and/or operational measures, that can be adopted individually or collectively to provide safety.
Considerations for flame resistant personal protective equipment (PPE), as a risk control measure, should only be adopted as a last resort principle. The document provides an assessment process and there is also a commentary on recognized standards and test methods for PPE in Appendix 2.
The Factfile points out that when carrying out a risk assessment, as a minimum we must:
- Identify what could cause injury (hazards). This is derived from system parameters such as voltage, fault level and electrical protection arrangements.
- Decide how likely it is that someone could be harmed and how seriously (the risk). This is derived from system conditions such as the condition of the equipment, the quality of the installation, measures used to contain an arc during switching under normal and fault conditions, how well it has been maintained and whether it is being operated in accordance with its original design. Importantly, it is also directly related to the task to be performed.
- Take action to eliminate the hazard, or if this isn’t possible, control the risk. The document highlights the use of the 4P approach, mentioned previously, to eliminate or control the risk.
The 4P approach to arc flash risk assessment will ensure that the three steps above are fulfilled. That will be through a quantitative prediction of the hazard and then through prevention to eliminate or significantly minimize the risk. Process, policies and procedures are then used to further reduce the likelihood and finally, personal protection against residual risk if needed.
The following model is used to describe how these steps can be implemented. The cycle matrix diagram shown illustrates how the important first step of Predict is used to calculate the severity of the arc hazard. This is followed by Prevent in that we apply the principles of prevention and order the risk control measures in a hierarchy. The next step is Process, policies and procedures where we apply the building blocks of safe procedures, safe places and safe people. The final step is Protect which looks at providing PPE as a last resort which, if the previous three steps have been correctly applied, will deal with residual risk only and lead to more lightweight solutions.
Figure 2: Diagram illustrating the 4P approach to arc flash risk assessment
By applying the 4P principles, it has been shown repeatedly that the need for PPE has been removed entirely or reduced to a comfortable and unrestrictive level. Let me give an example.
Figure 3: Clean room
Back in 2007, I carried out an arc flash study for a high-tech manufacturer of computer hard drive recording heads. There were 1,400 staff employed there including 140 electrical maintenance staff and 4 electrical contracting companies. Much of the manufacturing took place in high-specification clean rooms and the study identified high incident energy levels in 120 control panels in these areas alone. It wasn’t feasible to simply protect individuals with PPE because of the lack of, and expensive nature of, clean room arc flash PPE at that time. The application of the 4P principles successfully reduced the incident energy levels at all the panels to less than 1.2 cal/cm2 at a working distance of 450 mm by applying new protection settings, refeeding some circuits from alternative sources, installing local HRC switch fuses and upgrading MCCBs in existing panels to more precise instantaneous settings.
NOTE: 1.2 cal/cm2 is a widely used threshold denoting a 50 % chance of the onset of a minor partial thickness burn.
That was, of course, preceded by the introduction of new safety rules and training to remove the need for working near to live conductors in the first place. The ‘in house’ team were then trained in the use of modelling software so that all future additions and alterations could be assessed at design stage.
The question is, if it was possible to apply the 4P principles to reduce the reliance on PPE because of the cost and availability of clean room arc rated PPE, why can’t this be the case for all environments?
The European Arc Flash Guide
The principles outlined in the IET Arc flash risk management Factfile are broadly based upon my book, The European Arc Flash Guide, which I would recommend for anyone requiring a comprehensive study of the management of arc flash in a UK/European context. It is available from the IET Library for IET members and from most bookstores.
Figure 4: The European Arc Flash Guide
The mission is to “Inform and influence duty holders, designers and service providers to reduce danger from electrical arcing, by providing quick, simple, accessible and accurate predictive tools coupled with practical advice.”
The book is essential reading for anyone responsible for designing or putting workers to task on, or near, large power electrical systems and is especially relevant where local health and safety law uses a risk-based approach to electrical safety such as in the UK and Europe. It is based upon a bedrock of risk management methodology using the 4Ps of Predict, Prevent, Process and Protect to ensure that arc flash hazards are systematically identified, analyzed, and prevented from causing harm. There are chapters that are dedicated to myths and mysteries as well as separate chapters for electrical utilities, duty holders, service providers, contractors, legislation and data collection.
Alongside the book, there is a set of calculators and charts that require a small subscription to give access to tools to allow simple but accurate prediction of hazard severity. These can be accessed online through www.ea-guide.com and can be managed from phones, tablets and PCs. The purpose of the calculators and accompanying charts is not to provide complex software calculations of entire electrical networks, but rather to help the reader to do dynamic risk assessments on a case-by-case basis.
List of arc flash tools
- IEEE 1584 Incident Energy Calculator.
- LV Circuit-Breaker Calculator.
- Incident Energy HRC Fuse Charts.
- LV Devices (Fuses and MCBs) up to 125 A Calculator.
- DC Incident Energy Calculator.
- Blast Pressure Calculator.
- DGUV Box Test Algorithm Calculator.
- Prospective Short Circuit Current Calculator Tool.
- LV HRC Fuse Time Current Curve Tool.
- IDMT Time Current Curve Calculator.
- Risk Assessment Form.
Registration with the EA-Guide site will give free online access to all the step-by-step written instructions and videos plus the first seven chapters of The European Arc Flash Guide.
NFPA 70E Standard for Electrical Safety in the Workplace
The American National Standard, NFPA 70E Standard for Electrical Safety in the Workplace, is often quoted within the UK as a means of managing the arc flask risk and has been cited in some of the comments on LinkedIn that were referred to previously. I would, therefore, like to clarify that duty holders should be very careful when considering use of the standard.
Like all NFPA (National Fire Protection Association) codes and standards, NFPA 70E is based upon a consensus-based process. First published in 1979, it was created at the request of the Occupational Safety and Health Administration (OSHA) of the United States of America Department of Labor.
Whilst the document is creditable in many ways, there needs to be caution when applying this consensus document in the UK. Issues such as energized electrical working permits fly in the face of the current UK guidance, Electricity at Work: Safe Working Practices, HSG85, which states: “An electrical permit-to-work is primarily a statement that a circuit or item of equipment is safe to work on and it has been isolated and, where appropriate, earthed. You must never issue an electrical permit-to-work for work on equipment that is still live or to authorise live work.”
That said, the standard has, in recent years, promoted hazard elimination and dead working as the first priority in the implementation of safety related work practices. I first presented a paper on Electrical Safety and Arc Flash in Europe alongside Jim Phillips to the IEEE Electrical Safety Workshop over 12 years ago in Daytona Beach, Florida. The paper included the UK/European style hierarchy of risk controls and three years later, this was adopted into NFPA 70E.
The document has useful information that a discerning UK electrical engineer would find useful when considering the arc flash hazard. But beware that the document is written for those countries that follow a US electrical safety model and the differences with the UK legislation could lead to confusion. For instance, energzied work is still permitted by NFPA 70E where the employer can demonstrate that “the task to be performed is infeasible due to equipment design or operational limitations”. Regulation 14 from the Electricity at Work Regulations 1989 would arguably present a much tougher test of reasonableness in allowing live work to proceed. In addition, NFPA 70E relies on American standards only such as ASTM, ANSI and UL. The UK regulations, British Standards and IEC standards for issues such as PPE, fault current estimation, design of electrical installations, shock protection boundaries, operation of electrical installations, electrical test equipment, labelling, signs and signals are all very different. That includes many of the electrical definitions that we use.
The advice is, if considering the implementation of any part of NFPA 70E, to ensure that it is incorporated into UK style safety rules and amended with caution. Competent advice should be sought where necessary.
Relevant UK legislation and HSE guidance including Northern Ireland
The following is a list of UK legislation that is pertinent to arc flash risk management. This is not exhaustive but provides a basis for discussion with comments shown in bulleted italics.
The Electricity at Work Regulations 1989 (NI 1991) (EAWR) are made under the Health and Safety at Work etc Act 1974* the purpose of which is to require precautions to be taken against the risk of death or personal injury from electricity in work activities. The following guidance is free of charge through the HSE website, https://www.hse.gov.uk.
*NOTE: The primary legislation in Northern Ireland is the Health and Safety at Work (Northern Ireland) Order 1978.
The Electricity at Work Regulations 1989 Guidance HSR25, published October 2015. The purpose of this guidance is to highlight what can be done by duty holders to achieve electrical safety compliance with the duties imposed by the regulations. In respect of the design of electrical installations, HSR25 states “BS 7671 is a code of practice which is widely recognised and accepted in the UK and compliance with it is likely to achieve compliance with relevant aspects of the Electricity at Work Regulations 1989.”
- In respect of specific arc flash design considerations, this is a forum in which willing individuals can engage to improve new innovative solutions through the IET.
Regulation 11 of the EAWR, “Means for protecting from excess of current”, says that “efficient means, suitably located, shall be provided for protecting from excess of current every part of a system as may be necessary to prevent danger.”
- Whilst HSR25 cites the difficulties in protecting against arcing currents as a possible defence in criminal proceedings, they can be predicted with much more accuracy in recent years and so the goal should be to disconnect such faults quickly and remove the danger.
Electricity At Work: Safe Working Practices, HSG85 (Third Edition), published 2013. The guidance covers the key elements to consider when devising safe working practices and is for people who carry out work on or near electrical equipment. There is a requirement that, “if there is a risk of burns from arcing or flashover that cannot be avoided, consider the use of adequately rated, thermally insulating, flame-resistant PPE”.
- In respect of the determination of adequate ratings, consult the IET Arc flash risk management Factfile and/or The European Arc Flash Guide.
The need for risk assessment comes from the Management of Health and Safety at Work Regulations 1999 (NI 2000) (MHSWR), the process for which was first established in 1992. Regulation 3(1)(a) states “Every employer shall make a suitable and sufficient assessment of the risks to the health and safety of his employees to which they are exposed whilst they are at work.”
- Whilst the Electricity at Work Regulations (EAWR) predates this, the risk assessment process is still required for electrical hazards. Is the arc hazard being identified as part of a risk assessment process?
In addition, Regulation 7 of MHSWR requires employers to ensure that people who have health, safety and welfare responsibilities in the workplace are competent. This includes appointing people to assess risks under Regulation 3 of the Management Regulations. Where the organization does not have the competence to manage health and safety in-house, “for example, if it's large, complex or high risk,” they can get help from a consultant or adviser.
- Are those undertaking arc flash risk assessments competent?
Regulation 4 of the Personal Protective Equipment at Work Regulations 1992 (as amended 2022) (NI 1993) introduces the last resort principle, and that engineering controls and safe systems of work should be considered first. The guidance on the regulations HSE L25, sets out the hierarchy of risk controls.
- Can the arc flash hazard be eliminated and if not, how can the risk be controlled so that harm is unlikely?
Regulation 4 of the PPE Regulations also requires that PPE takes account of ergonomic requirements and the state of health of the person or persons who may wear it and that it is effective to prevent or adequately control the risk or risks involved without increasing overall risk.
- Have these factors been considered bearing in mind the restrictive nature of very heavy PPE?
Conclusions
- Carry out a risk assessment using the tools that are available to understand the severity of the hazard and the risk. Secondly, take action to eliminate the hazard, or if this isn’t possible, control the risk. Make sure that control measures follow a hierarchy putting elimination of the hazard first and that those control measures follow the local secondary legislation.
- The greatest prevalence of arc flash injuries is among electrically qualified workers. Therefore, it is important that this group of workers are made aware of the hazard and the safeguards.
- Use the IET Factfile on Arc flash risk management as an appreciation of the principles of arc flash risk assessments. For a deeper understanding, consult The European Arc Flash Guide.
- Exercise caution when considering the implementation of NFPA 70E into UK facilities and seek competent advice where necessary.
Mike Frain Bio
Mike Frain is the author of The European Arc Flash Guide and expert for the British Standards Institute and International Electrotechnical Commission (IEC) TC 78: Live Working Committees. He is the Convener for the Arc Flash Working Group (TC 78 WG 15) and the Team Leader for the IEC Arc Flash End User Guidance Project Team. He is the Secretary for the IET South Yorkshire Local Network, and former Vice Chair of the IET Engineering Safety Policy Panel and led the IET Arc Flash Working Group. He is a Chartered Engineer, a Fellow of the Institution of Engineering and Technology, and a Corporate Member of the Chartered Management Institute.